Handformguss: Qualitäts- und Umweltvorteile dank schwefelreduziertem Bindersystem
Die Umstellung auf ein neues Bindersystem für die Form- und Kernherstellung ist für eine Gießerei eine echte Herausforderung. Sie bedeutet eine tiefgreifende Veränderung eines bestehenden Prozesses und wird nur vorgenommen, wenn man sich deutliche Vorteile verspricht. Mit dem Ziel, ihre Position im Segment anspruchsvoller Gussqualitäten auszubauen, nahm die Metallwerk Franz Kleinken GmbH in Dorsten diese Herausforderung an. In Zusammenarbeit mit dem Gießereichemie-Unternehmen Hüttenes-Albertus führte Kleinken ein schwefelreduziertes Furanharz-Bindersystem ein, das in Sachen Qualität und Umwelt punktet.
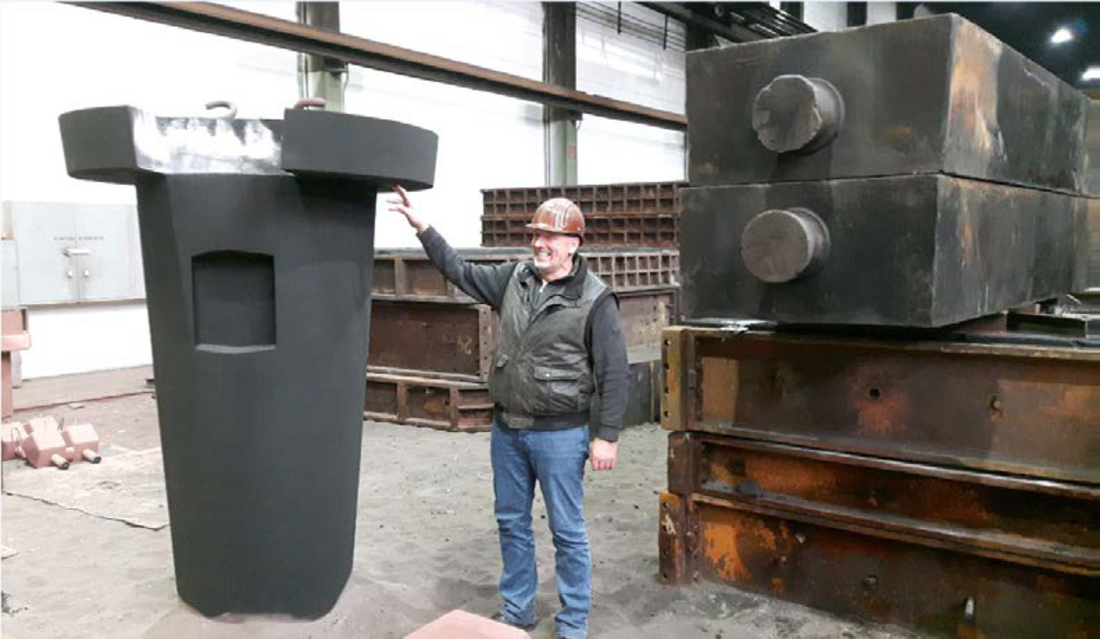
Die Firma Kleinken produziert anspruchsvollste Gussstücke für nahezu alle Industriebereiche. Das Spektrum reicht von Präzisionsteilen für Gas- und Dampfturbinen oder Pumpen bis hin zu Komponenten für den Kraftwerksbau sowie die Lebensmittelindustrie. Zu den Spezialitäten gehören auch thermobeständige Bauteile, die im Warmbereich von 200° bis 600° C zum Einsatz kommen. Alle Erzeugnisse der Gießerei können im eigenen Hause komplett fertig bearbeitet werden, sodass der Kunde einbaufertige Produkte aus einer Hand bekommt.
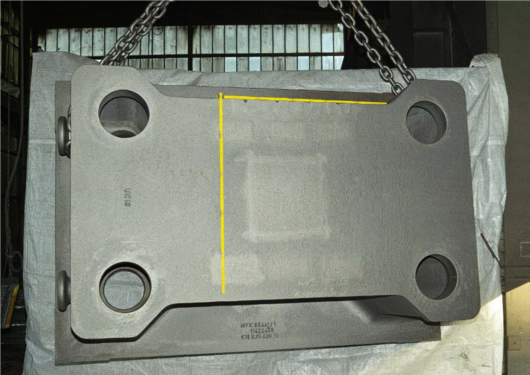
Seit 1921 hat Kleinken seine Kompetenzen rund um den Guss ständig weiterentwickelt. Das Unternehmen erzeugt und bearbeitet heute mit 140 Beschäftigen etwa 4.000 Tonnen Guss, oftmals für Kunden, die von weit her kommen, um genau hier ihren „Guss nach Maß“ zu erhalten, der für ihre hochwertigen Endprodukte erforderlich ist. Bis zu 30 Tonnen bringen die Gussteile aus den Werkstoffen Grau-, Sphäro- und Vermikularguss auf die Waage - und erfüllen dabei strengste Qualitätskriterien.
Für ihre anspruchsvollen, hochwertigen Gussprodukte fordern die Kunden immer häufiger die Herstellung nach den amerikanischen ASTM-A Standards (American Society for Testing and Materials). Dies beinhaltet spezielle Methoden zur Überprüfung mechanischer Werte und der Oberflächenbeschaffenheit, welche höchsten Anforderungen genügen müssen. So wird zum Beispiel das Grundgefüge (Matrix) per Ultraschall auf Lunker oder Einschlüsse überprüft. Die Qualität der Oberfläche wird mithilfe einer Magnetpulverprüfung oder Farbeindringprüfung beurteilt.
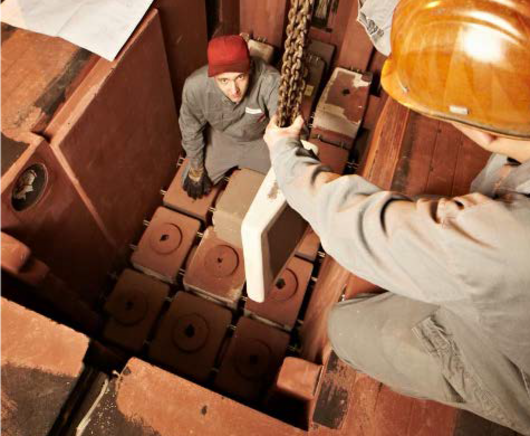
Gemeinsame Lösungsentwicklung
Um Gussstücke für das Premiumsegment Sphäroguss bis 20.000 kg prozesssicher herstellen zu können, plante das Metallwerk Kleinken die Umstellung auf ein neues Bindersystem für die Form- und Kernherstellung. Namhafte Zulieferer gießereichemischer Produkte wurden gebeten, geeignete Lösungsvorschläge zu unterbreiten. Dank kompetenter Beratung und intensiver Zusammenarbeit mit der Gießerei gelang es Hüttenes-Albertus, eine geeignete Problemlösung anzubieten.
Für die Entwicklung dieser Lösung arbeiteten die Fachleute von Kleinken und Hüttenes-Albertus eng zusammen: Auf eine Ist-Analyse des Prozesses sowie der Altsandwerte in der Gießerei folgten umfangreiche Untersuchungen im HA-Labor, bei denen die Biegefestigkeit des Formstoffs ermittelt und verglichen wurde. Aufgrund der überzeugenden Ergebnisse erfolgte dann sehr schnell die Umstellung auf das neue Bindersystem.
Bei dem Metallwerk Kleinken handelt es sich um eine reine Handformgießerei. Es werden keine Großserien-Produkte gefertigt, sondern nach Kundenauftrag individuelle Gussstücke oder Kleinserien.
Formen und Kerne für die oftmals schwierig darzustellenden Gussteile werden ausschließlich von – größtenteils im eigenen Haus – ausgebildeten Facharbeitern gefertigt und montiert. Bedingt durch die Größe der Gussteile und die Fertigung nach Maß setzt Kleinken bei der Form- und Kernherstellung auf ein kalthärtendes Verfahren, auch No-Bake-Verfahren genannt. Kernherstellungsverfahren, bei denen die Aushärtung mithilfe von Gas oder durch Hitze erfolgt, sind für die großen und dickwandigen Gussstücke aus technischen Gründen nicht geeignet.
Beim No-Bake-Verfahren wird der Formgrundstoff in Durchlaufmischern mit einem Bindemittel sowie einer Säure vermischt, welche als Katalysator bzw. Härter fungiert. Hüttenes-Albertus, ein führender Hersteller von Kunstharzbindemitteln für Gießereien, bietet bereits seit Jahrzehnten Kaltharzsysteme für die Fertigung von Formen und Kernen für den Groß- und Einzelguss an. Diese Produkte wurden und werden immer wieder weiterentwickelt, um die wachsenden Anforderungen der Gießereien und ihrer Kunden zu erfüllen.
Modifiziertes Furanharz erlaubt verringerten Schwefelanteil im Härter
Bei dem Bindersystem, für das sich die Firma Kleinken entschieden hat, handelt es sich um ein modifiziertes Furanharz, das besonders reaktiv ist, in Kombination mit einer Säure, die, bedingt durch die hohe Reaktivität des Binders, weniger Schwefel benötigt. Der Furfurylalkohol als wesentliche Komponente des Furanharzes reagiert unter saurer Katalyse mit sich selbst, polymerisiert und härtet aus. Spezielle Inhaltsstoffe machen das Harz besonders reaktiv, wodurch eine Reduktion des Schwefelgehalts im Säurekatalysator ermöglicht wird.
Ein höherer Schwefelanteil hat unter anderem den Nachteil, dass es zu einer Schmelze-Formstoff-Reaktion kommen kann. In deren Folge treten flächenhaft pockennarbenartige Aufrauungen und Vertiefungen an der Gussoberfläche auf. Diese „Orangenhaut“ ist oft mit einem weiß-bläulich erscheinenden Belag behaftet, der aus faserförmigem SiO2 besteht. Am anfälligsten für diesen Fehler ist Gusseisen mit Kugelgraphit. Er kommt besonders bei dickwandigen Teilen vor, also an mittleren bis schweren, aber auch an sehr kompakten Gussstücken. Am stärksten sind dabei die Stellen belastet, an denen das Metall lange flüssig bleibt und somit lange Reaktionszeiten und eine hohe Formstoffaufheizung gegeben sind. Im Bereich der Randzone kann es außerdem zu Graphitentartungen kommen.
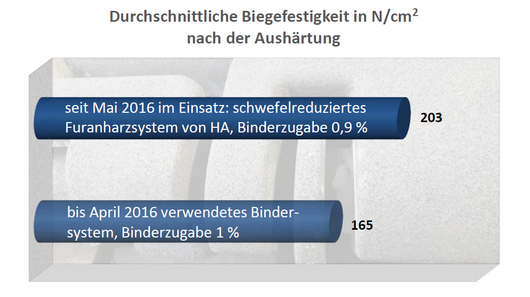
Deutlich verbesserte Oberflächen
Das schwefelreduzierte HA-Furanharz-System (bestehend aus dem Kaltharz 8500 und den Aktivatoren 7901, 7674 und 7809), das die Gießerei Kleinken inzwischen einsetzt, liefert hingegen deutlich verbesserte Oberflächen. Gleichzeitig sind wichtige Parameter wie die Verarbeitungszeit des Formstoffs und die Aushärtungszeit optimal eingestellt.
Das neu eingeführte Bindersystem hat zudem einen positiven wirtschaftlichen Aspekt: Die Harzzugabe konnte von 1 % auf 0,9 % gesenkt werden, während sich die Festigkeit von Formen und Kernen sogar erhöht hat (siehe Abbildung 1). Die geringere Binderzugabe geht einher mit einer Verringerung der Emissionen beim Abgießen. Dies wirkt sich vorteilhaft auf Arbeitsumgebung und Umwelt aus. Darüber hinaus konnte noch ein weiterer Effekt beobachtet werden: Durch die verringerte Bindermenge ist der Formstoff fließfähiger und kann besser verdichtet werden. Gasfehler oder Vererzungen treten somit seltener auf.
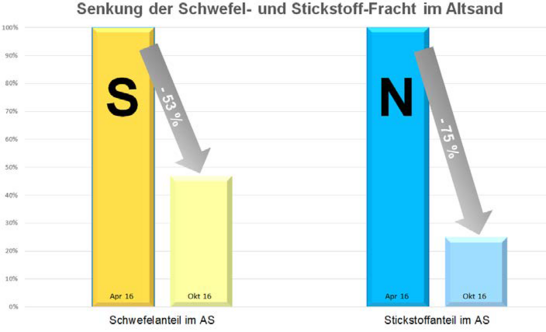
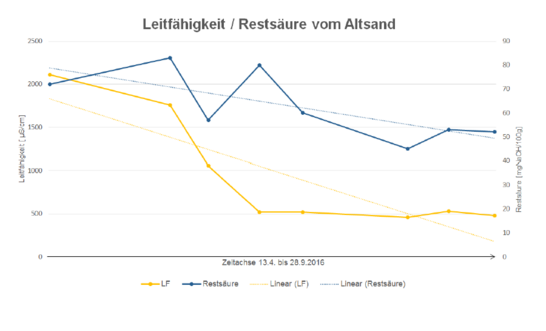
Wie die Abbildung 2 zeigt, konnten über den Zeitraum von April bis Oktober 2016 (also sechs Monate während der Umstellung) die bekannten Störelemente in Furan- Altsanden Schwefel (S) und Stickstoff (N) signifikant reduziert werden konnten. Dies ist durch den Systemwechsel sowie durch die Einsparung bei den Zugabemengen zu erklären.
Die Grafik 3 (Leitfähigkeit und Restsäure) untermauert den unmittelbar einsetzenden Trend, dass durch die „milden“ Aktivatoren die Salzfracht an der Sandkornoberfläche verringert und somit die Leitfähigkeit reduziert wird. Auch die sauren Bestandteile, ausgedrückt durch den Wert Restsäure, konnten kontinuierlich abgebaut werden.
Umwelt- und Kostenvorteil: weniger Neusand erforderlich
In puncto Umweltverträglichkeit spielt auch das Thema Altsand eine wichtige Rolle. Formgrundstoffe, die mit Furan-No-Bake-Bindern verfestigt wurden, lassen sich sehr gut wieder aufarbeiten und mehrfach für die Form- und Kernherstellung wiederverwenden. Es muss nur darauf geachtet werden, dass der Schwefelanteil, der sich mit der Zeit im Formstoff anreichert, einen festgelegten Richtwert nicht überschreitet. Dann muss ein Teil durch Neusand ersetzt werden. Enthält ein Bindersystem weniger Schwefel, erfolgt diese Anreicherung langsamer; der recycelte Sand kann länger im Kreislauf verbleiben und die Neusandzufuhr reduziert werden. Vergleichende Analysen belegen, dass der Schwefelgehalt im Altsand sich mit dem neuen Bindersystem nahezu halbiert hat. Dies schont die Umwelt und trägt zu einer Senkung der Deponiekosten bei.
„Das neue System, das wir in Zusammenarbeit mit Hüttenes-Albertus eingeführt haben, bietet eine hohe Prozesssicherheit“, berichtet Gießereileiter Frank Weber. „Das bedeutet, dass wir im Segment der besonders hochwertigen Gusswerkstoffe die hohen Anforderungen unserer Kunden leichter erfüllen und unseren Prozess besser steuern können. Gleichzeitig beobachten wir positive wirtschaftliche und umwelttechnische Effekte, die uns als Gießerei wichtige Vorteile bringen.“
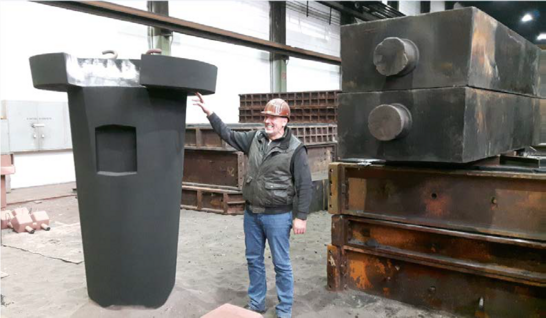
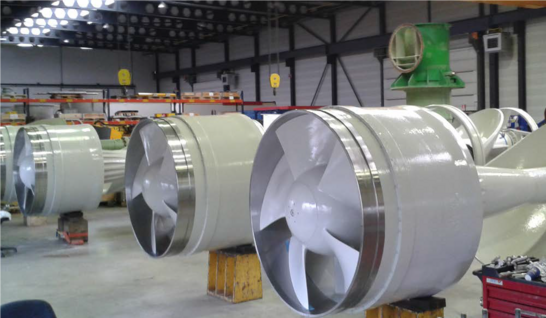
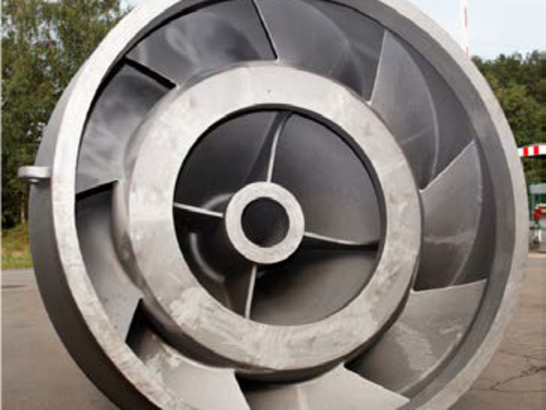
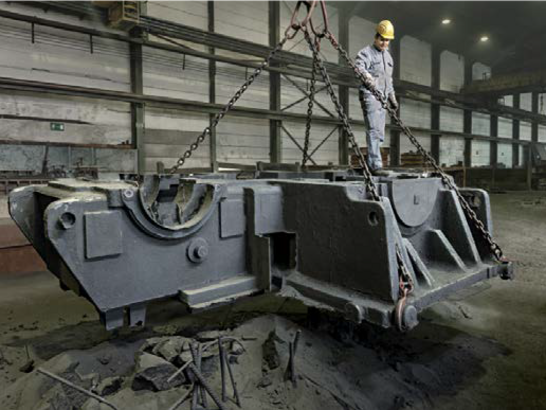
Veröffentlicht: Februar 2017
Ansprechpartner bei HA zum Thema Kaltharz-Systeme:
Christian Fourberg
E-Mail