Hand moulding – quality and environmental advantages thanks to low-sulphur binder system
Converting to a new binder system for mould and core production is a real challenge for any foundry. It involves a substantial change to an existing process and is only done with the promise of clear benefits. With the aim of expanding its position in the supply of highly-specialised castings, the Dorsten-based metal and iron foundry, Franz Kleinken GmbH, took up this challenge. In co-operation with the foundry chemicals company Hüttenes-Albertus, Kleinken launched a low-sulphur furan resin binder system, which delivers both quality and environmental gains. Sabine Umla-Latz of Hüttenes-Albertus reports on the project.
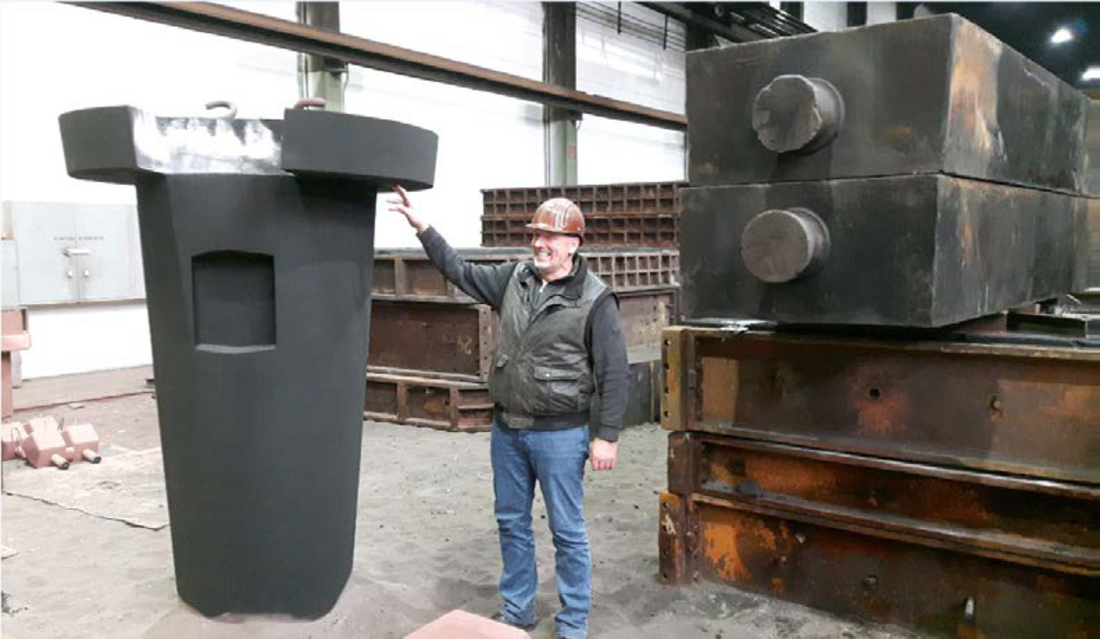
Kleinken produces highly-specialised cast parts for almost every industry sector. The portfolio ranges from precision parts for gas and steam turbines or pumps, to components for power plant construction and the food industry. Specialties also include thermally resistant components, which are used in high temperature applications of 200-600°C. All foundry products can be completely finished inhouse, providing customers with readymade products from a single source. Since 1921, Kleinken has continually developed its casting expertise. Today, the company, with 140 employees, produces and processes around 4,000 tonnes of castings, often for customers from all over the world who come to get exactly the ‘custom cast’ required for their high-quality end products. Their cast parts made of grey, SG and vermicular cast iron weigh up to 30 tonnes, while meeting the strictest quality criteria. For their high-precision, high-quality castings, customers are increasingly demanding compliance with the ASTM-A standards. These standards set by the American Society for Testing and Materials include special methods for testing mechanical properties and surface finish, which must meet the highest requirements. For example, ultrasound is used to check the basic structure (matrix) for cavities or inclusions. Surface quality is assessed by magnetic particle inspection or dye penetrant testing.
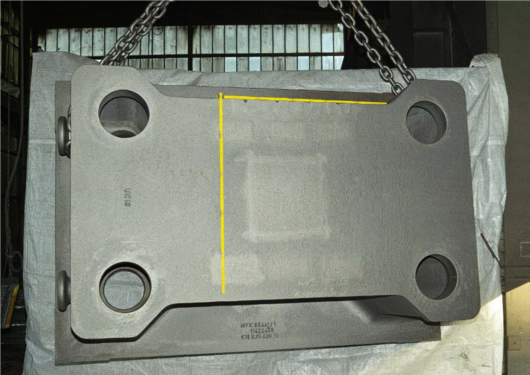
Joint development of solutions
To enable reliable production of up to 20,000kg cast parts for the premium segment of SG iron, the Kleinken metalwork plant planned to switch to a new binder system for mould and core production. The experts from Kleinken and Hüttenes-Albertus worked closely together to develop a solution. An analysis of the current process and the used sand levels in the foundry was followed by extensive testing in the HA laboratory, during which the bending strength of the moulding material was determined and compared. Due to the persuasive results, the changeover to the new binder system took place very quickly. Kleinken is a pure manual moulding foundry – it does not produce large-series runs, rather sticking to customised cast parts or small batches on customer order. Moulds and cores for castings, which are often difficult to model, are manufactured and assembled exclusively by skilled craftsmen – mostly in-house built. As a result of the cast part size and the customised production process, Kleinken has opted for a cold-curing process, also called no-bake process, during mould and core production.
Core production processes involving gas or heat curing are not suitable for large and thick-walled castings for technical reasons. In the no-bake process, the moulding base material is mixed in flow mixers with a binder and an acid, which acts as a catalyst or hardener. Hüttenes-Albertus, a leading producer of foundry resin binders, has, for decades, been offering cold-curing systems for mould and core production for large-scale and single cast parts. These products have been and will continue to be developed to meet the growing demands of foundries and their customers.
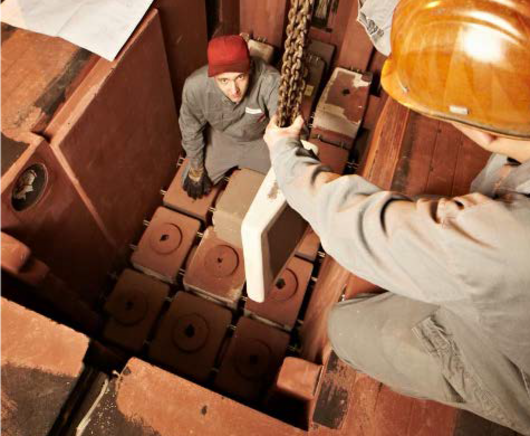
Modified furan resin helps to reduce sulphur content in hardeners
The binder system chosen by Kleinken is a modified, extremely reactive, furan resin in combination with an acid that requires less sulphur due to the binder’s high reactivity. The furfuryl alcohol, as an essential component of the furan resin, reacts with itself during acid catalysis, polymerises and hardens. Special ingredients make the resin particularly reactive, which allows a reduction in the sulphur content in the acid catalyst. One of the disadvantages of an increased sulphur content is a potential reaction of the melt with the mould material. This leads to the formation of extensive pockmark-like roughening and recesses on the casting surface. This ‘orange peel’ texture is often covered with a whitebluish film layer, which consists of fibrous SiO2. SG cast iron is most prone to this defect. It occurs predominantly in thick-walled parts, i.e. in medium to heavy, but also in very compact cast part. The areas most strongly affected are the ones where the metal remains liquid for long periods of time and is therefore exposed to long reaction times and a high heating of the moulding material. In the area of the rim zone, graphite degeneration may also occur.
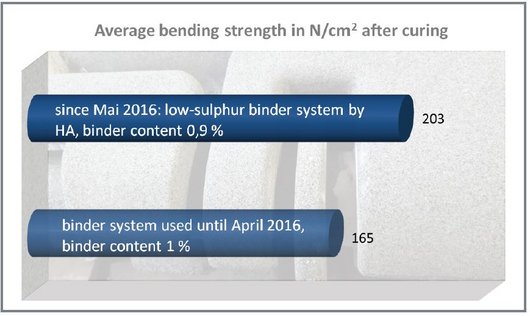
Surfaces clearly enhanced
The low-sulphur HA furan resin system (consisting of cold resin series 8500 and series 7901, 7674 and 7809 activators), which is now used by the Kleinken foundry, provides significantly improved surfaces. At the same time, important parameters such as the processing time of the moulding material and the curing time have been optimally set. The newly introduced binder system also has a positive economic aspect – resin addition could be reduced from one to 0.9 per cent, while at the same time increasing the strength of moulds and cores (see fig.3). The lowered addition of binder goes hand in hand with a reduction in emissions during casting. This has benefits for both the working environment and the natural environment. In addition, another effect has been observed; due to the reduced amount of binder, the moulding material is more flowable and can be better compacted. Gas defects or mineralisation occur less frequently.
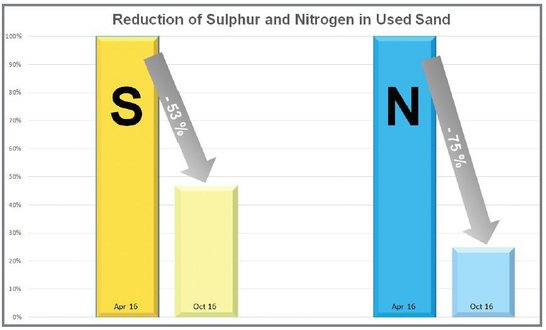
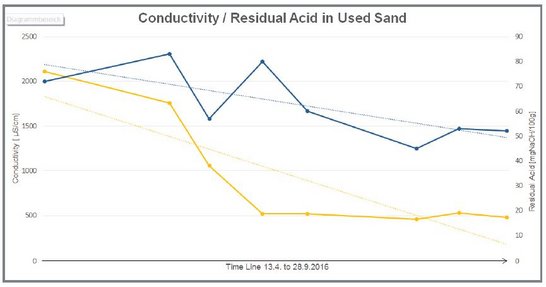
As shown in fig.4, sulphur (S) and nitrogen (N), known as interfering elements in recycled furan resin sand, could be significantly reduced over the period from April to October 2016 (i.e. the six months during changeover). This can be explained by the system change as well as by the savings in the quantity added. Fig.5 (conductivity and residual acid) confirms the immediate trend that the ‘mild’ activators progressively reduce the salt load on the sand grain surface and thus reduce conductivity. The acidic components, as expressed by the value of residual acid, could also be continuously reduced.
Environmental and cost benefits – less new sand required
The topic of used sand plays an important role in environmental compatibility. Moulding materials solidified with furan no-bake binders is very well suited for recycling and can be reused several times for the production of moulds and cores. However, care must be taken to ensure that the sulphur content, which accumulates over time in the moulding material, does not exceed a fixed threshold. If it does so, then some has to be replaced by new sand. With a low-sulphur binder system, this accumulation takes place more slowly; the recycled sand can remain in circulation longer and the addition of new sand can be reduced. Comparative analyses show that the sulphur content in recycled sand has almost been halved with the new binder system. This protects the environment and helps reduce landfill costs. “The new system, which we introduced in co-operation with Hüttenes-Albertus, offers a high level of process reliability”, reports Frank Weber, foundry manager. “This means that we are able to meet the high requirements of our customers more easily in the segment of particularly high quality castings while achieving better process control. At the same time, we are seeing positive economic and environmental effects, which bring us important advantages as a foundry.”