Bleiben Sie informiert
Hier finden Sie Aktuelles rund um Hüttenes-Albertus und interessante Fachbeiträge von unseren Experten.
Gießerei und Gießereichemie arbeiten Hand in Hand
Bauteile, insbesondere für den Antriebsstrang in der Elektromobilität, werden immer filigraner und komplexer, der Grad der Automatisierung steigt, neue Legierungen kommen zum Einsatz und verschärfte Umweltauflagen erschweren zunehmend die Einhaltung von Grenzwerten. Mit diesen wachsenden Anforderungen an die Gießereien steigen auch die Ansprüche an die gießereichemischen Produkte. Moderne emissionsreduzierte Sandbinder können hier einen wichtigen Beitrag zur Verbesserung der Gesamtsituation leisten.
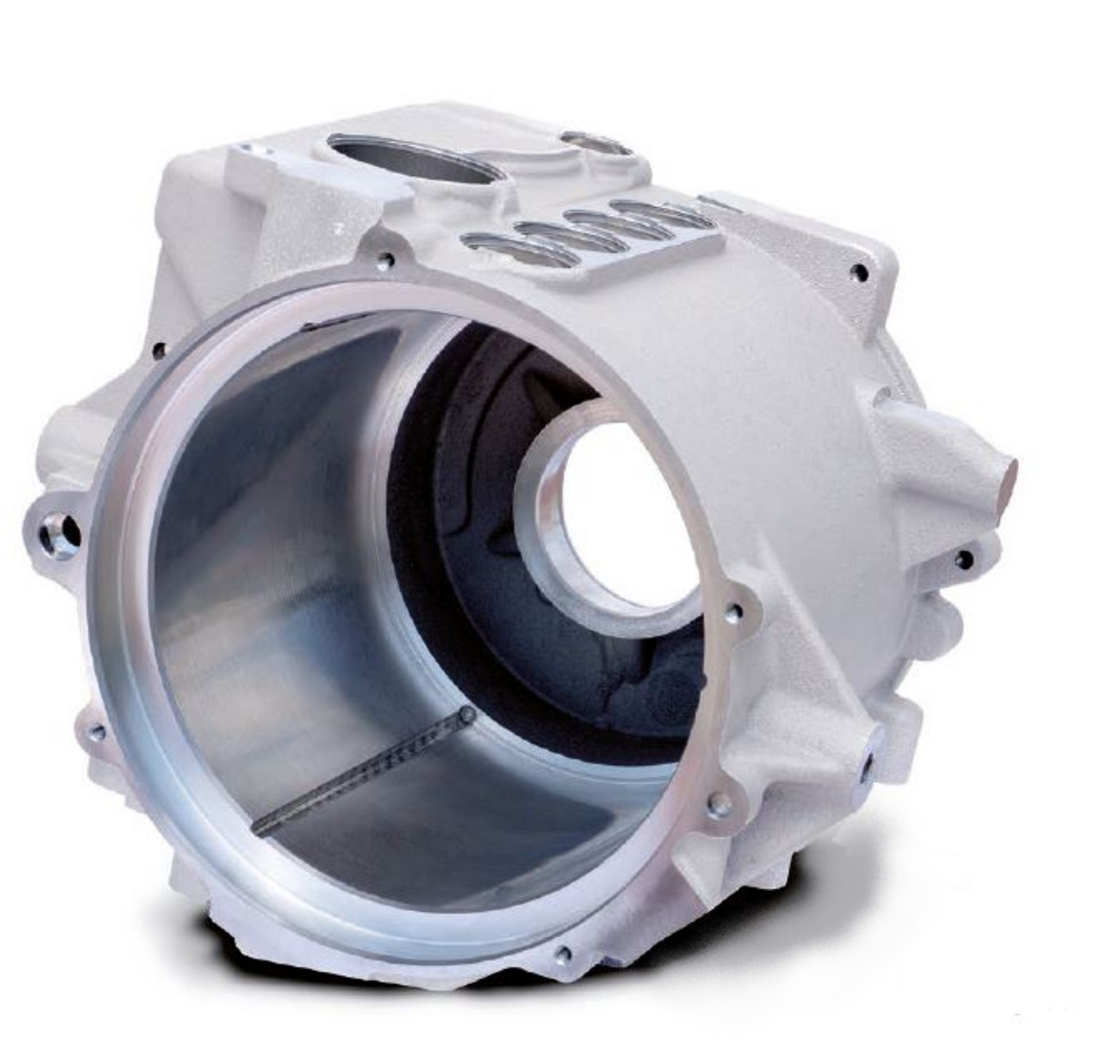
Bauteile werden immer komplexer und Gusswandstärken geringer. Damit steigen die Kernintensität und die Anforderungen an die eingesetzten Kernbindersysteme. Weitere Entwicklungen der letzten Jahre sind der zunehmende Grad der Automatisierung und die Einführung neuer Legierungen, zudem wurden und werden Auflagen und Umweltgesetze weiter verschärft. All diese Tendenzen sind auf nationaler und auch europäischer Ebene spürbar. Die Einhaltung von Emissionsgrenzwerten wird zunehmend schwerer. Vor dem Hintergrund der Reduzierung der Treibhausgasemissionen und der Teilnahme am Handel mit CO2-Emissionszertifikaten ist auch die Gießerei-Industrie aufgefordert, den Gesamt-CO2-Ausstoß zu verringern. In der Gießerei- und Zulieferindustrie werden aus diesem Grund möglichst kohlenstoffarme Produkte eingesetzt. Zusätzlich leiden viele Gießereien an der mangelnden Akzeptanz durch die Anwohner. Häufig gibt es Beschwerden aufgrund von Geruchs- und Lärmbelästigung. Dazu befinden wir uns mitten in der Umgestaltung der Automobilproduktion, weg vom Verbrennungsmotor, hin zur Elektromobilität. Diese Transformation ist mit vielen Veränderungen und Risiken für die Gießerei-Industrie verbunden. Sie bietet aber auch Chancen, insbesondere für die hochentwickelten deutschen Gießereien. Moderne emissionsreduzierte Bindemittel spielen hierbei eine wichtige Rolle.
Aufgabenstellung für die Gießereichemie
Um die gestiegenen ökologischen Anforderungen zu erfüllen, reduzieren Gießereichemie und Gießereien den Einsatz organischer Stoffe. Um kostenintensive Sekundärmaßnahmen wie Abgasreinigungsanlagen oder thermische Nachverbrennung zu vermeiden bzw. zu minimieren, ergeben sich grundsätzlich zwei Wege:
> Einsatz von anorganischen Bindersystemen,
> Einsatz von organischen Bindemitteln mit anorganischen Bestandteilen.
Die technologischen und wirtschaftlichen Voraussetzungen erlauben es momentan noch nicht, flächendeckend auf anorganische Bindersysteme umzusteigen. Das Cold-Box-Verfahren ist aufgrund seiner vielfältigen Anwendungsmöglichkeiten, seiner Effektivität und auch seiner technisch-technologischen Weiterentwicklung nach wie vor das dominierende Kernherstellungsverfahren.
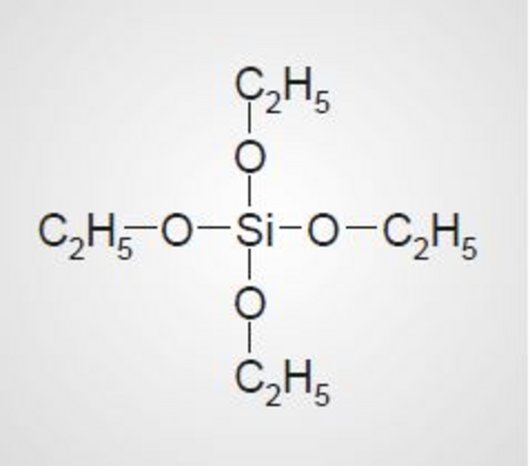
Moderne Cold-Box-Systeme
Mit der Anwendung der ersten Cold-Box-Systeme mit Anteilen von teilweise anorganischen Lösemitteln im Jahr 1999 begann Hüttenes-Albertus (HA) als innovativer Gießereizulieferer frühzeitig damit, Cold-Box-Bindersysteme mit verbesserten umweltrelevanten Eigenschaften für Gießereien zu entwickeln. Gegenüber den bisher im Cold-Box-Verfahren verwendeten aliphatischen und aromatischen Lösemitteln war der Einsatz des Tetraethylorthosilikats (TEOS) der erste Schritt in Richtung eines Cold-Box-Systems mit anorganischem Charakter (Bild 1).
Bild 1: TEOS (Tetra-EthylOrthoSilikat)
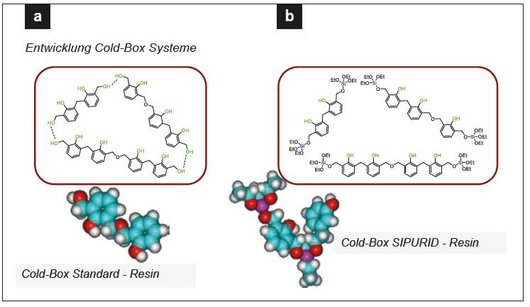
a) Standard-Cold-Box-Harz, b) Sipurid Harz
Das Sipurid-Cold-Box-System
Das angestrebte Ziel war, schrittweise den Anteil der anorganischen Bestandteile im Cold-Box-System zu erhöhen: HA entwickelte deshalb eine neue Bindergeneration auf Basis von Tetraethylsilikat. Beim Sipurid-System sind die anorganischen Einheiten nicht nur im Lösungsmittel enthalten, sondern auch im Harzmolekül integriert. Diese patentierte Innovation ist ein Meilenstein in der Entwicklung neuartiger Cold-Box-Systeme, weil hier erstmals die Vorteile des Cold-Box-Verfahrens mit denen der Anorganik kombiniert werden. Die Integration der anorganischen Einheiten erfolgt durch eine Substitutionsreaktion, bei der die Hydroxylgruppen der Harzmoleküle mit Ethylsilikaten zur Reaktion gebracht werden (Bild 2).
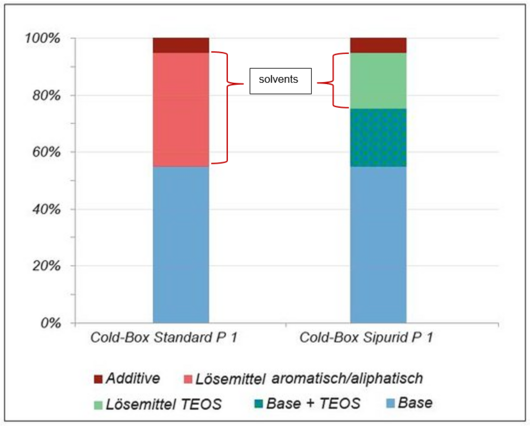
Hierbei nimmt die Größe der Harzmoleküle zu, sodass die Menge des eingesetzten Aktivators im Verhältnis zum Harz reduziert werden kann. Überraschenderweise ist trotz höherer Molekularmasse die Viskosität des Grundharzes reduziert. Dadurch wird es möglich, deutlich weniger Lösemittel einzusetzen als bei den bisher bekannten Cold-Box-Harzen (Bild 3).
Das Sipurid-System bildet aufgrund des hohen Anteils an anorganischen Bestandteilen die Brückentechnologie auf dem Weg zur anorganischen Kernfertigung. Der Kohlenstoffgehalt konnte im Vergleich zu den aromatischen Cold-Box-Systemen um mindestens 20 Prozent gesenkt werden. Durch den konsequenten Einbau von anorganischen Komponenten hat die Sipurid-Bindergeneration bereits einen beachtlichen Anorganikanteil von 12,4 Prozent erreicht (Bild 4). Die weitere Verbesserung der Umweltverträglichkeit und Schadstoffminimierung war das Hauptentwicklungsziel des Sipurid-Systems. Durch seine geringe Organikfracht werden sehr geringe Benzol-, Gas- und Kondensatmengen emittiert. Ein weiterer großer Vorteil besteht in der deutlichen Verringerung der Qualmbildung beim und nach dem Gießen.
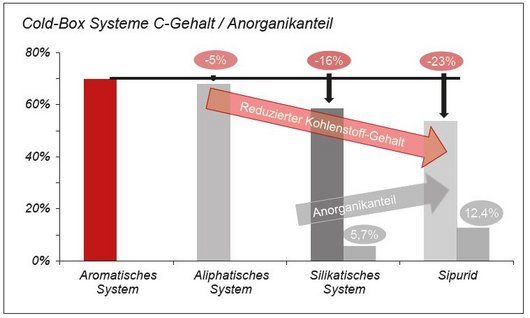
E-housing mit optimaler Funktionsintegration
Am Beispiel eines einbaufertig hergestellten wassergekühlten Elektromotorgehäuses (s. Aufmacherbild) der Firma DGH Sand Casting lassen sich Herausforderungen und Lösungsmöglichkeiten sowie die Synergieeffekte einer Entwicklungspartnerschaft zwischen Gießerei und Gießereichemie sehr gut zeigen. Das Unternehmen DGH Sand Casting am Standort Friedrichshafen produziert seit 1913 für anspruchsvolle Kunden zuverlässig und flexibel viele Millionen hochwertiger Gussteile. Es verfügt über ein umfassendes Sandguss Know-how und deckt ein sehr breites Produktspektrum ab.
Ausgangslage und Anforderungen
Aufgrund des Kostenziels bei gleichzeitig enger Terminschiene kam nur das Gießen in Sand als Verfahren infrage. Es bietet darüber hinaus eine sehr hohe Gestaltungsfreiheit bei begrenztem Änderungsaufwand bezüglich Zeit und Kosten. Wichtig war dem Kunden ein korrosionsfestes Gehäuse in der Legierung GAlSi7Mg0,3 AC 42100, die höchste Integration von Funktionen durch den Einsatz von Kernen, die nahezu unendliche Gestaltungsmöglichkeiten und dennoch hohe Leistungsdichte bei niedrigstem Bauraumbedarf (realisiert durch geringe Wandstärken) ermöglichen. Bestmöglichste Kühlung durch eine „raue“ Wassermantel-Oberfläche, beste Wärmestabilität im Anfahrbetrieb sowie die Integration des Getriebeölhaushaltes mit Temperierung waren weitere Anforderungen.
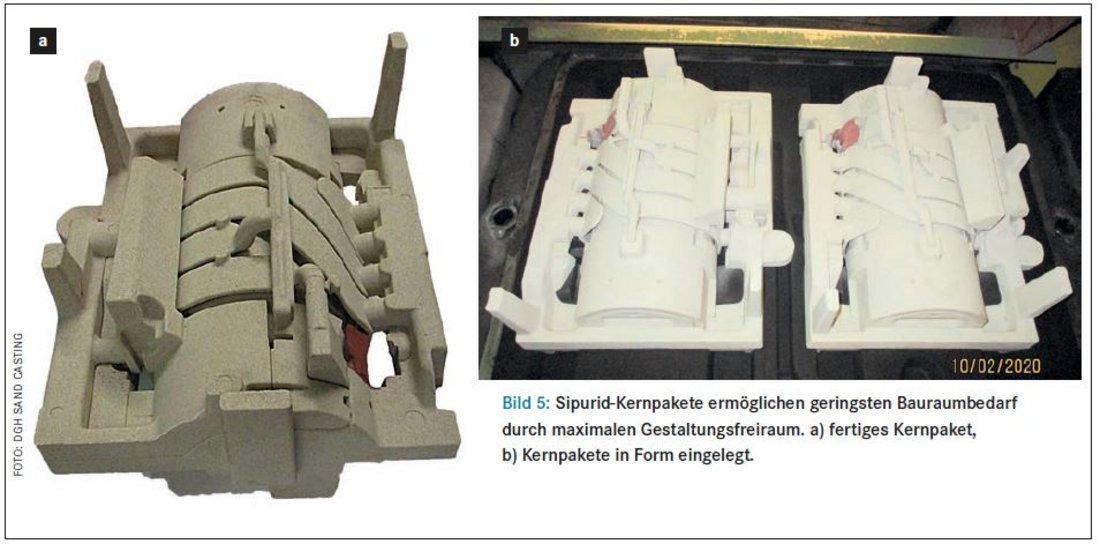
Die Lösung
Die DGH-Lösung integriert die Wasser- und Ölkühlung in einem Gehäuse. Das bedeutet geringster Bauraumbedarf durch maximalen Gestaltungsfreiraum im Sandgießverfahren (Bild 5). Die mechanische Bearbeitung im Stator-Raum wird durch zylindrische Kerne erleichtert. Aufgrund verringerter Werkzeug-Bauzeiten verkürzen sich die Entwicklungszeiten und die Werkzeugkosten liegen niedriger als bei den Dauerformverfahren. Die Korrosionsbeständigkeit und die mechanischen Kennwerte erreichen ein gutes Niveau.
Gießtechnische Umsetzung
Das Elektromotor-Gehäuse wurde 2019 als „Gussteil mit der besten Funktionsintegration“ mit dem Newcast-Award ausgezeichnet. Die erfolgreiche gießtechnische Umsetzung beruht auf:
- geringsten Wandstärken, um niedriges Gewicht zu erreichen
- Positionierung der Sandkerne zur optimalen Kühlung mittels Wassermantel
- Gießsimulationen, um eine gelenkte Erstarrung zu realisieren
- Legierungsauswahl für Korrosionsbeständigkeit
- Füllsimulation für Kernkästen
Innovation des Sipurid-Systems
Das vorher eingesetzte Bindersystem „vernebelte“ regelmäßig die Produktionshalle, insbesondere im Bereich der Auspackstelle. DGH Sand Casting suchte deshalb nach Optimierungspotenzial bei der Qualmbildung. Nach Einführung des Sipurid-Systems verbesserte sich die Situation in der Halle deutlich. Im Vergleich zu Standard-Cold-Box-Systemen zeigt das Sipurid-System eine höhere thermische Stabilität und eine geringere Deformationsneigung (Bild 6).
Diese wünschenswerten Eigenschaften sprechen für sich und überzeugten auch die Gießerei. Durch den Einsatz des Sipurid-Systems wurden die Toleranzen bei den deformationskritischen Wassermantelbereichen deutlich besser eingehalten (Bild 7).
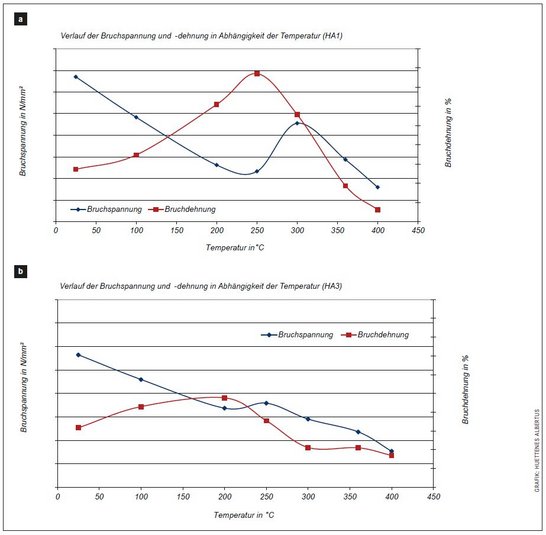
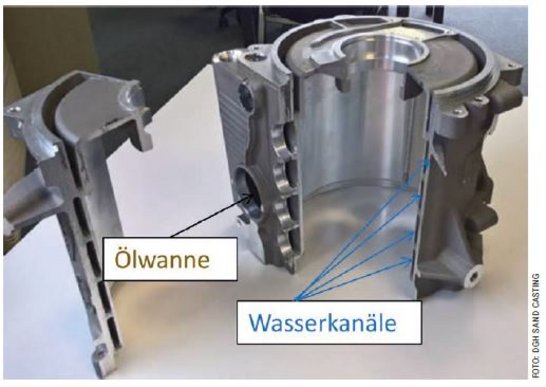
Fazit und Ausblick
Durch die exzellente technologische Arbeit bei DGH Sand Casting und die Entwicklungspartnerschaft mit HA wird das komplexe Bauteil nun zuverlässiger und in verbesserter Qualität produziert. Das Beispiel „Elektromotor“ zeigt ganz hervorragend die erfolgreiche Bewältigung neuer Anforderungen in der Gießerei-Industrie. Das Sipurid-System wird kontinuierlich, immer orientiert an neuen Herausforderungen, seit seiner Einführung systematisch weiter verbessert. Unser Dank gilt der Firma DGH Sand Casting für die intensive Zusammenarbeit, die Bereitstellung der Daten und die Möglichkeit der Veröffentlichung.
Dezember 2020
Autoren:
Peter-Michael Gröning, Regional Product Manager EMEA Cold-Box Systems, Hüttenes-Albertus Chemische Werke, Düsseldorf
Florian Piehler, Techn. Projektleiter AV & Simulation, DGH Sand Casting Production GmbH & Co. KG, Friedrichshafen, www.dgh-sandcasting.de