Multitasking: Schlichten für den Schleuderguss
Die Bedeutung von Schlichten beim Schleudergießprozess wächst mit ihren Aufgaben. Dienten Schlichten früher vor allem als Trennschicht zwischen Kokille und Gussstück, erfüllen sie heute gezielt ganz spezielle Anforderungen: Innovative Schlichten für das Schleudergießen helfen Gussfehler zu vermeiden, beeinflussen mechanische Parameter und dienen sogar als formendes Medium, mit dem besondere Oberflächenstrukturen erzeugt werden können.
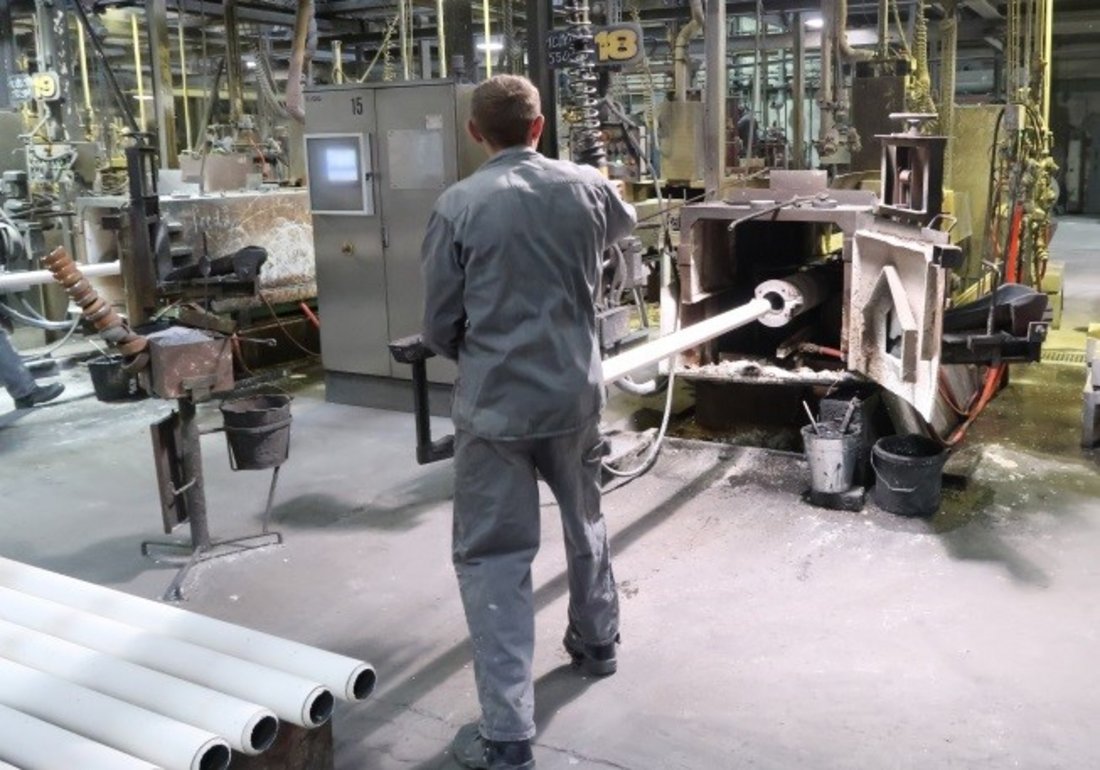
Prozessbeschreibung Schleuderguss
Der Prozess des Schleudergießens ist ein Verfahren, das Mitte des 19. Jahrhunderts schon von dem britischen Ingenieur und Erfinder Sir Henry Bessemer angewandt wurde und zur Fertigung rotationssymmetrischer Gussstücke dient. Beim Schleudergießen wird die Schmelze in eine Metallkokille gegossen, welche sich mit hoher Geschwindigkeit um ihre Mittelachse dreht. Die dabei wirkenden Zentrifugalkräfte pressen die Schmelze an die Kokillenwand und erzeugen ein sehr reines und hochverdichtetes Gefüge.
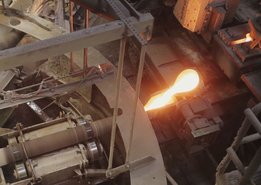
angeordnet werden.
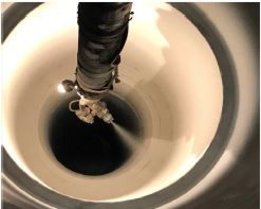
Kokille mit einer Schlichte ausgekleidet.
Das Metall erstarrt, während sich die Kokille dreht – mit dem Vorteil, dass ohne die Verwendung von Speisern ein lunkerfreies Gussstück in Form eines rotationssymetrischen (Hohl-)Körpers entsteht. Die innere Geometrie der Kokille bestimmt dabei die Außenkontur des Gussteils, die zugeführte Metallmenge die Wanddicke.
Beim Horizontalguss wird die Schmelze in eine liegende Kokille eingegossen. Für besonders lange Gussstücke oder beim kontinuierlichen Schleuderguss kann die Gießrinne während des Gießprozesses verschoben werden.
Beim Vertikalguss erfolgt der Abguss in einer Kokille, deren Achse vertikal rotiert. Vertikalguss wird zum Beispiel für konische oder kugelförmige Außenkonturen eingesetzt. Die Umdrehungsgeschwindigkeit ist hierbei oft deutlich langsamer als beim Horizontalguss.
Meist wird die Kokille beim Schleuderguss mit einer keramischen Schutzschicht, der sogenannten Schlichte, ausgekleidet. Seit der Entwicklung des Schleudergießverfahrens haben sich die Anforderungen an die Gussstücke und parallel dazu die Aufgaben der Schlichte immer mehr erweitert. Mithilfe moderner Schleuderguss-Schlichten können heute ganz gezielt bestimmte Eigenschaften und Vorteile erzielt werden. Die verschiedenen Aufgaben, die eine Schleuderguss-Schlichte erfüllen kann, sollen im Folgenden beschrieben und anhand praktischer Einsatzbeispiele illustriert werden.
Schlichte als Trennstoff
Der Schlichteauftrag kann durch einstreuen eines trockenen Pulvers in die rotierende Kokille erfolgen.
Ein weiteres häufiger angewandtes Verfahren ist der Schlichteauftrag durch das Einsprühen einer Schlichtedispersion in die Kokille. Die Hauptaufgabe ist dabei eine Trennwirkung zwischen Kokille und Schmelze zu erzielen. Pulverschlichten können z.B. aus Mischungen von Ferrosilizium, Graphit, Quarzstaub, Bentonit oder Kieselgur bestehen. Die Zugabe von Wasser und eines Dispersionsmittels ermöglicht das Aufstreichen oder Sprühen der Schlichte. Die gleichmäßige Beschichtung der Kokillenwand sorgte für ein leichteres Ziehen des Gussteils und für eine längere Lebensdauer der Kokille.
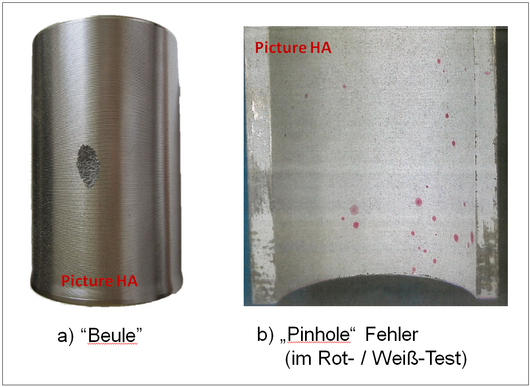
bei.
Vermeidung von Gussfehlern
Gussfehler wie Einschlüsse, Gas- oder Reaktionsfehler, die allein durch die Änderung der Prozessparameter nicht vollständig vermieden werden konnten, sind ein großes Problem in diesem Gießprozess.
Da die metallische Dauerform beim Schleuderguss gasundurchlässig ist, übernimmt die Kokillenschlichte eine wichtige Funktion beim „Gasmanagement“. Zur Vermeidung von Gasfehlern wie Pinholes muss die Schlichte eine gewisse Porosität aufweisen und in der Lage sein, entstehende Zersetzungsgase aufzunehmen.
Durch eine gezielte Optimierung der Zusammensetzung und Struktur der Schlichte können Gussfehler wirksam vermieden werden. Ersetzt man zum Beispiel organische Bestandteile durch anorganische, oder verwendet man kalzinierte Rohmaterialien, erreicht man eine Verringerung des Glühverlustes und damit des Risikos von Gasfehlern. Durch die Auswahl von Rohstoffen mit geringer Reaktivität kann außerdem das Risiko von Reaktionsfehlern reduziert werden.
Isolierende Wirkung
Ein wichtiger Faktor für die Gefügeausbildung und den Härteverlauf ist die Isolierwirkung der Schlichte. Sie regelt die Geschwindigkeit des Wärmeübergangs vom flüssigen Metall auf die Kokille und trägt damit zur Steuerung der Erstarrung und des Gussgefüges bei.
Die Isoliereigenschaften hängen einerseits von der Zusammensetzung der Schlichte und andererseits von der Schichtdicke auf der Kokille ab. Beide Parameter beeinflussen signifikant die Abkühlgeschwindigkeit der Schmelze und folglich die mechanischen Eigenschaften des Gussteils. Diese wiederum sind ein entscheidender Bestandteil der Kundenanforderungen. Insbesondere bei dünnwandigen Rohren müssen gezielt isolierende Eigenschaften eingestellt werden, um eine gute Bearbeitbarkeit zu gewährleisten.
Die Auswahl geeigneter Rohstoffe hat Einfluss auf die Wärmeleitfähigkeit, aber auch auf Faktoren wie chemische Reaktivität, Feuerfestigkeit, Härte und Anwendungseigenschaften der Schlichte. Auch die Korngrößenverteilung ist von Bedeutung: Eine feine Körnung weist viele Korngrenzen auf und verlangsamt so die Wärmeleitung. Eine große Korngröße hingegen schafft mehr Hohlräume zwischen den einzelnen Körnern, was ebenfalls zu einer isolierenden Wirkung führt.
Feststoffanteil, Viskosität und rheologische Eigenschaften müssen so ausbalanciert sein, dass einerseits die gewünschte Schichtdicke erreicht wird, die Schlichte sich gleichzeitig aber auch gut sprühen und gleichmäßig auftragen lässt. Da es sich bei der Schlichte um eine Dispersion handelt, die sich bei der Lagerung wieder entmischen kann, ist vor der Anwendung eine entsprechende Aufbereitung erforderlich. Über die Bestimmung der Dichte bzw. Auslaufzeit wird die Schlichte vor ihrem Einsatz auf die gewünschte Verarbeitungsviskosität eingestellt.
Steuerung der Oberflächenbeschaffenheit
Da die meisten Gussteile nach der Produktion weiterbearbeitet werden, gibt es für viele Anwendungen keine speziellen Anforderungen an die Rauheit der Gussteil-Oberfläche. Für bestimmte Anwendungen sind Form und Höhe der Rauigkeit sehr klar definiert.
Dies gilt zum Beispiel für Abwasserrohre aus Grauguss: Bei ihrer Herstellung werden glatte Oberflächen angestrebt. Diese Anforderung hat zwar keinen direkten Einfluss auf die Funktionalität des Gusses, aber einige Gießereien betrachten sie als ein äußerlich sichtbares Qualitätskriterium, mit dem sie bei ihren Kunden punkten wollen.
Im Gegensatz dazu gibt es aber auch Kundenanforderungen, die gerade die Erzeugung einer rauen Oberfläche zum Ziel haben: Bei Zylinderlaufbuchsen ist eine raue Oberfläche mit einer genau definierten Oberflächenstruktur ausdrücklich erwünscht.
Schlichte als formgebender Faktor
Zylinderlaufbuchsen können in Motorblöcke eingepresst werden. Eine andere Möglichkeit ist, die Buchsen nach einer Bearbeitung in den Motorblock mit einzugießen. Mit der Weiterentwicklung von Gießverfahren und Schlichten können heute definierte Oberflächenstrukturen erzeugt werden, die es ermöglichen, die Buchsen direkt in den Motorblock einzugießen. Das flüssige Metall umfließt die strukturierte Oberfläche, füllt Vertiefungen und Hinterschneidungen aus, sodass die Materialien von Motorblock und Laufbuchse eine äußerst starke und belastbare Verbindung eingehen.
Ziel bei diesem Verfahren ist es, direkt beim Gießen eine raue Oberflächenstruktur zu erhalten, sodass die Außenseite der Zylinderlaufbuchse keiner weiteren Bearbeitung bedarf. Die Tiefe und Form der Struktur kann je nach Kundenspezifikation festgelegt werden. Möglich sind stachel- oder pilzförmige Erhebungen, aber auch Strukturen mit Hinterschneidungen. Die Strukturtiefen liegen je nach Kundenwunsch zwischen 0,3 und 1,1 mm.
Die Strukturen mit Hinterschneidungen können im Druckgussverfahren verarbeitet werden, während die Buchsen mit Igel- oder Pilzstruktur auch im konventionellen Kokillenguss verarbeitet werden können.
Neben der speziellen Einstellung einiger Maschinenparameter ist die Schlichte maßgeblich an der Gestaltung dieser Oberflächenstrukturen beteiligt. Man kann somit sagen, die Schlichte fungiert als formgebender Faktor (Formstoff).
Eine moderne Schlichte für Herstellung strukturierter Zylinderlaufbuchsen setzt sich zusammen aus speziellen Feuerfestmaterialien mit definierter Korngröße und -form, Wasser, Bindemittel, Dispergiermitteln und Tensiden zur Steuerung der Oberflächenspannung.
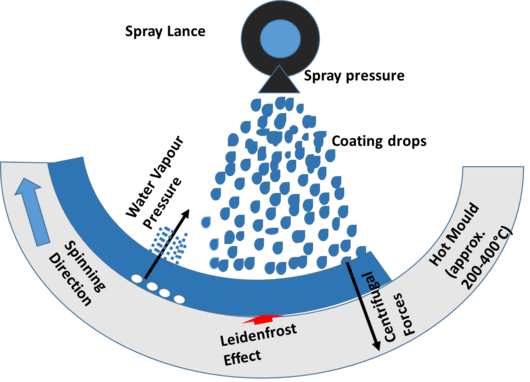
Skizze 1 zeigt schematisch die Vorstellung der verschiedenen Prozesse, die beim Sprühauftrag einer wässrigen Schlichte auf die heiße Schleudergusskokille auftreten.
Treffen die Schlichtetropfen auf die Kokille, so wird die Schlichte durch die Drehbewegung der Kokille beschleunigt und aufgrund der Zentrifugalkräfte gegen die heiße Kokille gepresst.
Sofort fängt das Wasser in der Schlichte an zu kochen. Es bilden sich aufgrund von Leidenfrost-Effekten Gasschichten bzw. Gasblasen.
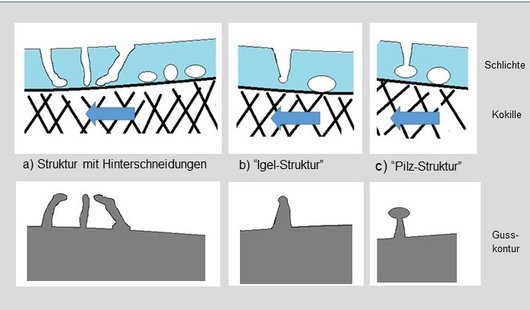
Mit fortschreitender Trocknung der Schlichte bilden sich Kanäle in der Schlichte aus. Skizze 2 skizziert das Konzept der Bildung verschiedener Strukturen aus den Gasblasen. Abhängig von der Schlichtezusammensetzung, den Zentrifugalkräften und der Kokillentemperatur bilden sich unterschiedliche Kanäle aus, die beim Guss wiederum zu den unterschiedlichen Oberflächenstrukturen führen.
Weitere Anforderungen an die Schlichte
Neben den zuvor beschriebenen Funktionen und Aufgaben einer Schleuderguss-Schlichte gibt es je nach Anwendung weitere Anforderungen:
Eine wichtige Eigenschaft im Hinblick auf die Arbeitsabläufe ist zum Beispiel das Ziehverhalten: Wenn das Rohr nach dem Erstarren aus der Kokille gezogen wird, soll die Schlichte daran haften und idealerweise vollständig mit aus der Kokille entfernt werden.
Für die Sauberkeit am Arbeitsplatz ist es wünschenswert, dass auf dem Gussteil eine zusammenhängende Schlichteschicht verbleibt, die möglichst wenig staubt. Wenn die Schlichte im nächsten Schritt abgestrahlt wird, muss sie leicht entfernbar sein – bei einer strukturierten Oberfläche ggf. auch aus den Hinterschneidungen. Aus Gründen des Arbeitsschutzes darf die Schlichte zudem kein kristallines Quarz enthalten.
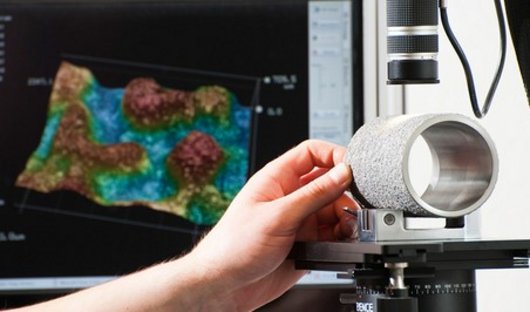
Gleichbleibende Qualität ist entscheidend
Um im Markt einen Vorteil gegenüber Wettbewerbern zu erzielen, sind viele Gießereien bestrebt, die Produktivität ihrer Prozesse zu erhöhen oder die Qualität ihrer Gussprodukte zu erhöhen. Dies führt zu immer engeren Prozessfenstern, mit dem Risiko, dass bereits kleinste Abweichungen großen Schaden nach sich ziehen können. Auch Schlichten müssen diese Anforderungen erfüllen. Es wird daher immer wichtiger, stabile Schlichteprodukte von gleichbleibender Qualität einzusetzen. Dies erfordert konstante Eigenschaften bezüglich Zusammensetzung, Viskosität und Applikationsverhalten. Nun finden bei der Herstellung von Schlichten auch natürliche Rohstoffe Verwendung, die in ihrer Qualität durchaus variieren können. Anhand umfassender Qualitätsprüfungen bei den Rohmaterialien können Abweichungen von vorgegebenen Eigenschaften frühzeitig erkannt werden.
Zusätzlich sollte eine regelmäßige Prozesskontrolle mithilfe geeigneter Messmethoden stattfinden. Beim Strukturguss ist auch die einheitliche Ausprägung der vom Kunden gewünschten Oberflächenstruktur Bestandteil der Qualitätsprüfung.
Innovationspotenzial für Gießer und Schlichteanbieter
Von der Automobil- über die Chemie- bis zur Papierindustrie; von Rohren über Walzen bis zu Buchsen: Wenn es um die Herstellung rotationssymmetrischer Bauteile geht, ist der Schleuderguss ein bewährtes Gießverfahren mit einem großen Anwendungs- und Innovationspotential. Für den Gießer lohnt es sich, bei der Prozessentwicklung für eine neue Schleuderguss-Anwendung frühzeitig das Know-how eines erfahrenen Schlichteanbieters hinzuzuziehen. Die Gießereifachleute und Chemiker bei HA greifen neue Herausforderungen gerne auf. Da es für spezielle Anwendungen oft kein Produkt „von der Stange“ gibt, wird eine Problemlösung Schritt für Schritt gemeinsam mit dem Kunden entwickelt und erprobt – von ersten Versuchen bis hin zur Serienreife.
Autoren: Dr. Klaus Seeger, Dr. Ekaterina Potaturina, Hüttenes-Albertus
Veröffentlicht: März 2019
Ihre Ansprechpartnerin bei HA zum Thema Schlichte:
Dr. Ekaterina Potaturina
E-Mail