From concept to component: The potential of sand casting in car body innovation
The "New Manufacturing World" congress took place for the first time on 11th and 12th of June. Professor Ferdinand Dudenhöffer and his team invited leading experts from the manufacturing industry to Böblingen. Ola Källenius, CEO of Mercedes-Benz, opened the congress, which provided a successful platform for international dialogue on all aspects of the automotive industry with a large number of speakers and panel discussions. In this environment, the HA Group and its co-operation partner Laempe had the opportunity to present their joint MEGA sandcasting project.
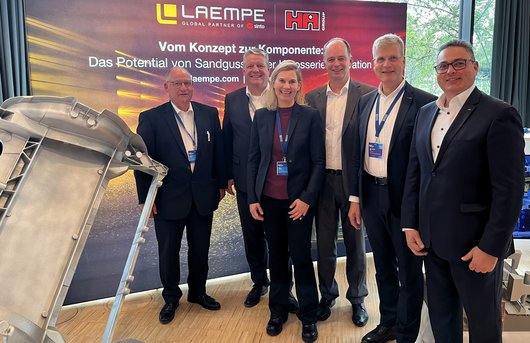
Foundry chemistry and core production - thinking ahead to the future together
What began some time ago as a casual exchange of ideas between two market leaders in their fields has now led to a concept with a concrete application example.
At the new "New Manufacturing World" congress, Rudolf Wintgens, Managing Director at Laempe Mössner Sinto, and Franz Friedrich Butz, Managing Director at HA, impressively demonstrated in their presentation on 12th of June 2024 how flexibly the proven sand casting process can also be used in the production of car body parts.
The automotive industry has been undergoing a substantial transformation for some years now, characterised in particular by a diversification in the powertrain. This is accompanied by an ever-increasing need to reduce weight, which has led to a significant increase in the use of aluminium castings in car body construction. This rapid development is leading to increasingly complex and larger structural components made from cast aluminium. Although die casting has established itself as an efficient process for the production of structural parts, the growing dimensions of the components are leading to increased investment requirements and technological challenges for the necessary die casting systems.
Sand casting could establish itself as an alternative, efficient and technologically more advantageous process. In an innovative study, two market leaders and a start-up are involved in researching its potential for car body construction. Sand casting is characterised by lower investment costs and many foundries already have some of the necessary production facilities, which could make it easier to switch to structural components. Sand casting enables a higher degree of design freedom and integration in component design through the mapping of cavities and undercuts for optimised component weights with the same or even better technical properties.
The study includes a concept for the production of a rear frame for a luxury-class vehicle using the core package low pressure die casting process. It also provides an economic and ecological comparison with the die casting process. The results indicate that sand casting can be a valid alternative to die casting, especially with increasing design complexity and increasing component size.
We are pleased about the great interest and the discussions that followed the presentation and will be happy to answer any questions you may have.
www.laempe.com www.ha-group.com