Multitasking: Coatings for Centrifugal Casting
As the range of centrifugal casting applications increases, so does the importance of coatings. In the past, coatings were mainly used as a separating layer between the mould and the casting part, whereas today they are designed to meet very specific requirements: Innovative coatings formulated for centrifugal casting help to avoid casting defects, influence mechanical parameters and even serve as a forming medium to allow the creation of special surface structures.
The centrifugal casting process
Centrifugal casting was first used in the middle of the 19th century by the British engineer and inventor Sir Henry Bessemer to produce rotationally symmetrical parts. In centrifugal casting, the melt is poured into a metal mould which rotates around its central axis at high speed. The centrifugal forces acting on it press the melt against the mould wall and produce a very pure and highly densified composite. The metal solidifies as the mould rotates –with the advantage that a cavity-free casting in the form of a cylindrical (hollow) body is produced without the use of feeders. The inner geometry of the mould determines the outer contour of the casting, the quantity of metal supplied determines the wall thickness.
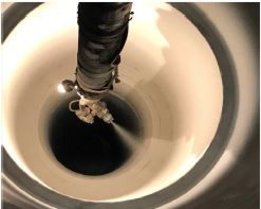
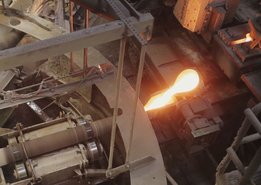
In horizontal casting, the melt is poured into a lying mould. In the case of particularly long castings or during continuous centrifugal casting, the runner can be moved during the casting process. In vertical casting, the casting takes place in a mould with a vertically rotating axis. Vertical casting can be used to produce conical or spherical outer contours. The rotational speed is often significantly slower than with horizontal casting. In centrifugal casting, the mould is usually lined with a ceramic protective layer, the so-called coating. Since the development of the centrifugal casting process, the demands placed on the casting parts and, at the same time, the functions to be met by the coating have continuously increased. Today, modern coatings for centrifugal casting make it possible to achieve clearly defined properties and advantages. The various functions that a centrifugal casting coating can perform are described below and illustrated using practical application examples.
Coatings as separating agents
The coating can be applied by sprinkling a dry powder into the rotating mould. An alternative frequently used process involves applying the coating by spraying a coating dispersion into the mould. The coating’s primary task is to achieve a separating effect between mould and melt. Powder coatings can, for example, consist of a mixture of ferrosilicon, graphite, quartz dust, bentonite or diatomaceous earth. The addition of water and a dispersion agent makes it possible to paint or spray the coating. The uniform coating of the mould wall makes it easier to extract the casting and extends the life of the mould.

Avoiding casting defects
Casting defects such as inclusions, gas or reaction defects, which cannot be completely eliminated simply by changing the process parameters, are a significant problem in the centrifugal casting process. As the metallic permanent mould is impermeable to gas during centrifugal casting, the mould coating plays an important “gas management” role. In order to avoid gas defects such as pinholes, the coating must have a certain porosity and be able to absorb the decomposition gases produced. By targeted optimisation of the com-position and structure of the coating, casting defects can be effectively avoided. If, for example, organic components are replaced with inorganic ones, or calcined raw materials are used, the loss on ignition and thus the risk of gas defects is reduced. Selecting raw materials with low reactivity also helps reduce the risk of reaction errors
Insulating effect
The insulating effect of the coating is an important factor in the composition formation and the hardness profile. It regulates the heat transfer from the molten metal to the mould, thus contributing to the control of solidification and the casting structure. The insulating properties depend on the one hand on the composition of the coating, and on the other hand, on the layer thickness on the mould. Both parameters have a significant impact on the cooling rate of the melt and consequently the mechanical properties of the casting. These, in turn, are a crucial component of customer requirements. Particularly with thinwalled pipes, insulating properties need to be specifically adjusted in order to achieve maximum workability. The selection of suitable raw mate-rials has an impact on thermal conductivity, but also on factors such as chemical reactivity, fire resistance, hardness and application properties of the coating. The grain size distribution is also important: a fine grain size has many grain boundaries and thus slows down heat transfer. A large grain size, on the other hand, creates more cavities between the individual grains, which also leads to an insulating effect. Solids content, viscosity and rheo-logical properties must be balanced in such a way that, on the one hand, the desired layer thickness is achieved while, at the same time, the coating is easy to spray on and allows an even application. Since the coating is a dispersion that may sediment out during storage, appropriate preparation is required before application. Before use, the coating is adjusted to the desired processing viscosity by deter-mining the density or efflux time.
Controlling surface textures
Since most castings are machined after production, there are no special requirements regarding the roughness of the casting surface for many applications. For certain applications, the shape and height of any roughness are clearly defined. This applies, for example, to grey cast iron wastewater pipes: during their manufacture, the aim is to achieve smooth cast surfaces. Although this requirement has no direct influence on the functionality of the casting, some foundries regard it as an externally visible quality criterion with which they want to score points with their customers. There are, however, also customer specifications that require the production of rough surface textures: For cylinder liners, a rough surface with a precisely defined surface structure is expressly desired.
Coatings as a forming medium
Cylinder liners can be pressed into engine blocks. It is also possible to cast the liners into the engine block after machining. With the further development of casting processes and coatings, it is now possible to produce defined surface structures that enable the liners to be cast directly into the engine block. The molten metal flows around the structured surface, filling in recesses and undercuts so that the engine block and liner materials form an extremely strong and resilient bond. The aim of this process is to obtain a rough surface structure during casting so that the outside of the cylinder liner does not require any further pro-cessing. The depth and shape of the structure can be determined according to customer specifications. Hedge-hog or mushroom-shaped elevations are possible, as are structures with undercuts. The structure depths vary between 0.3 and 1.1 mm, depending on customer requirements. The structures with undercuts can only be processed in pressure die casting, while the liners with hedgehog or mushroom structure can be processed in conventional gravity die casting. In addition to the special configuration of certain machine parameters, the coating plays a decisive role in achieving these surface structures. It can therefore be said that the coating acts as a forming factor (moulding material). A modern coating for the production of structured cylinder liners is composed of special refractory materials with defined grain sizes and shapes, water, binder, dispersion agent and surfactants to control surface tension.
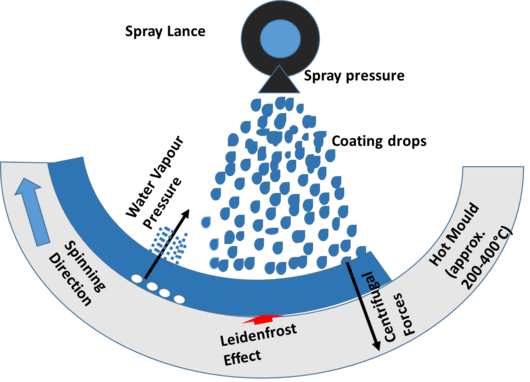
This Image shows the various processes that occur when an aqueous coating is sprayed onto the hot centrifugal casting mould. If drops of the coating hit the mould, the coating is accelerated by the rotary motion of the mould and pressed against the hot mould as a result of the centrifugal forces. The water in the coating immediately begins to boil. Leidenfrost effects cause gas layers or gas bubbles to form. As the coating dries, channels form in the coating.
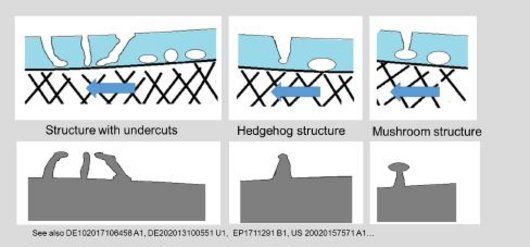
This image on the right side illustrates the concept of forming different structures from the gas bubbles. Depending on the coating composition, the centrifugal forces and the mould temperature, different channels are formed, which in turn lead to different surface structures during casting.
Additional coating requirements
In addition to the functions of coating for centrifugal casting described above, there are a number of additional, application specific requirements: A key characteristic with regard to the process steps is, for example, extraction behaviour: When the tube is extracted from the mould after solidification, the coating should adhere to the casting and, ideally, be completely removed from the mould with the casting. In terms of cleanliness in the work-place, it is also desirable that a contiguous layer of the coating remains on the casting, and that it is as dust-free as possible. If the next process step involves blasting, the coating should be easy to remove – in case of a textured surface it may also need to be removed from the undercuts. For health and safety reasons, the coating must not contain crystalline quartz.
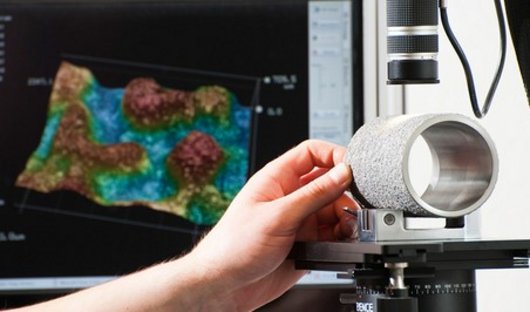
Consistent quality is crucial
In order to gain a competitive advantage, many foundries strive to increase the productivity of their processes and/or improve the quality of their castings. This leads to ever narrower process windows, with the risk that even the smallest defects can cause major disruption. Coatings must also meet these more demanding requirements. It is therefore becoming increasingly important to use stable coating products of uniform quality. Foundries need products with consistent properties in terms of composition, viscosity and application behaviour. However, natural raw materials are typically used in the production of coatings, and these can vary in their quality. Comprehensive quality testing of the raw materials enables deviations from specified properties to be detected at an early stage. In addition, regular process checks should be carried out using suitable measuring methods. In structural casting, the uniformity of the surface structure desired by the customer is also an integral component of the quality assurance process
Innovation potential for foundries and coating suppliers
From the automotive to the chemical and paper industries; from pipes to rolls to cylinder liners: when it comes to the production of rotationally symmetrical components, centrifugal casting is a proven, technically sophisticated casting process with enormous application and innovation potential. For foundries, it is well worth consulting an experienced coating supplier at an early stage in the development process of any new centrifugal casting applications. The foundry specialists and chemists at Hüttenes-Albertus are always happy to take on new challenges. Since there is often no “off-the-shelf” product for special applications, we develop and test solutions step by step together with our customers –from initial testing all the way through to series production readiness.