The foundry and foundry chemistry working hand in hand
A range of cast components, in particular those used in electric vehicle powertrains, are becoming increasingly intricate and complex: there is a high degree of automation, new alloys are being used, and stricter environmental regulations make it more and more difficult to comply with official limit values. As the challenges faced by foundries grow, so do the demands they place on foundry-grade chemical products. Modern low-emission sand binders can play a pivotal role in improving the overall situation.
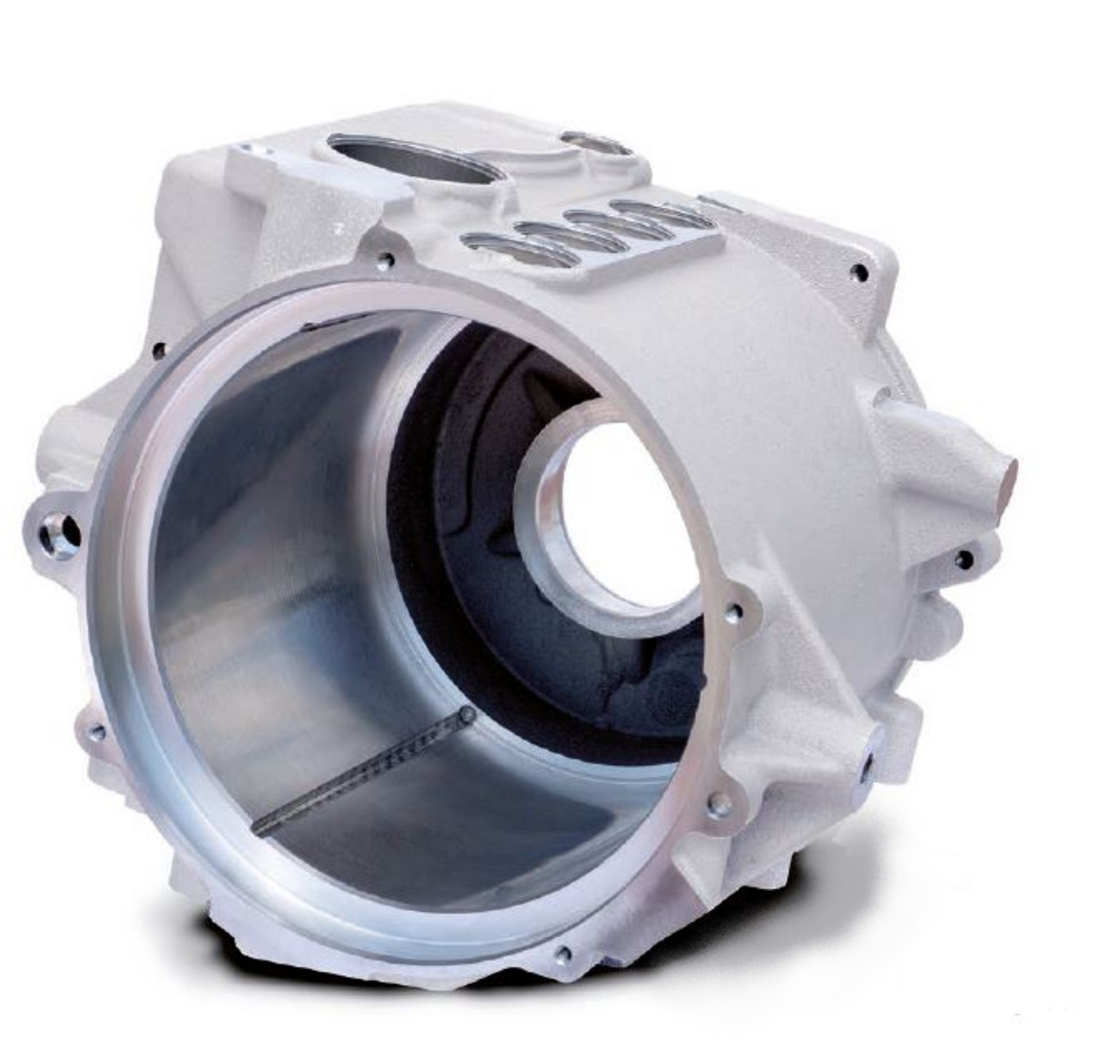
Components are becoming increasingly complex and wall thicknesses are becoming ever thinner. Growing complexity results in increased core intensity and higher demands on core binder systems. Other developments in recent years have included further advances in automation and the introduction of new alloys; in addition, directives and environmental standards imposed by regulatory authorities and legislators have been and are being further tightened. All these trends are noticeable at both a national and a European level. Compliance with emission limits is becoming increasingly challenging. Given requirements to reduce greenhouse gas emissions and participate in the EU’s CO2 emission certificate trading system, the foundry industry is no exception in having to reduce its overall CO2 emissions. As a result, the foundry industry and its suppliers have increasingly come to rely on low-carbon products. In addition, many foundries suffer from a lack of acceptance by local residents and are often subjected to complaints about odour and noise pollution. On top of all this, we now find ourselves in the midst of a revolution in automotive production, away from the internal combustion engine and towards electromobility. This transformation comes along with many changes and risks for the foundry industry. But it also offers opportunities, especially for highly developed foundries. Modern low-emission binders clearly have a pivotal role to play.
The challenges for foundry chemistry
In order to comply with ever stricter environmental standards, foundries and the foundry chemistry industry are reducing their dependence on organic substances. In order to avoid or minimise cost-intensive secondary measures such as waste gas purification plants or thermal afterburning, there are two basic approaches that can be adopted:
> Use of inorganic binder systems,
> Use of organic binders with inorganic components.
A comprehensive switch to inorganic binder systems is not yet technologically or economically viable. Thanks to its wide range of applications, its effectiveness and its further technical and technological development, the Cold-Box process remains the dominant method in core manufacturing.
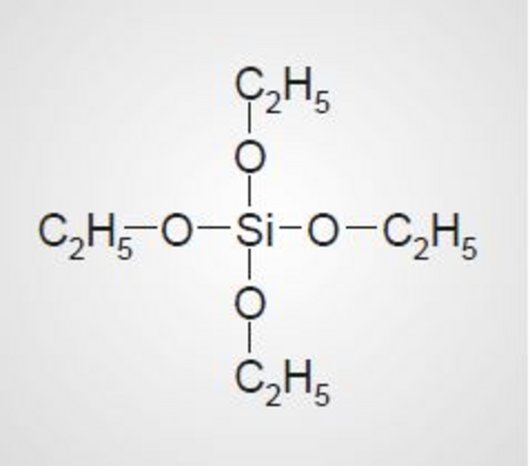
Modern Cold-Box systems
With the introduction of the first Cold-Box systems to use partially inorganic solvents in 1999, the innovative foundry supplier Hüttenes-Albertus (HA) was one of the first to develop Cold-Box binder systems with improved environmental properties for foundries. Compared to the aliphatic and aromatic solvents previously used in the Cold-Box process, the use of tetraethyl orthosilicate (TEOS) was the first step towards a Cold-Box system with inorganic components (Fig. 1).
Fig. 1: TEOS (tetraethyl orthosilicate)
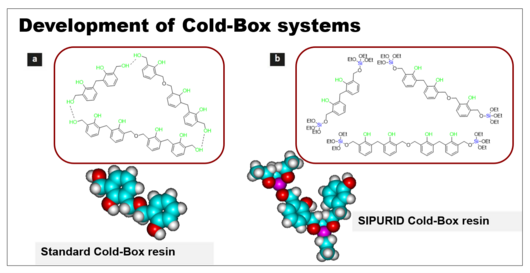
(a) Standard Cold-Box resin, (b) Sipurid resin
The Sipurid Cold-Box system
HA set itself the objective of gradually increasing the proportion of inorganic components in its new Cold-Box system and proceeded to develop a new generation of binders based on tetraethyl silicate. In HA’s Sipurid system, inorganic units are not only contained in the solvent, they are also integrated into the resin molecule. This proprietary innovation represented a milestone in the development of new Cold-Box systems, because it allowed the advantages of the Cold-Box process to be combined with the advantages of inorganics for the very first time. The integration of the inorganic components is achieved by a substitution reaction in which the hydroxyl groups of the resin molecules are reacted with ethyl silicates (Fig. 2).
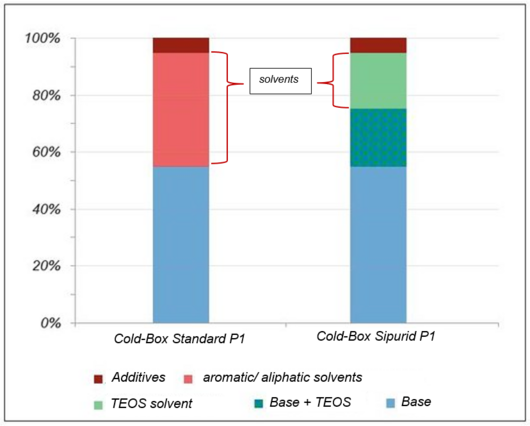
As a result of this process, the size of the resin molecules increases, allowing the amount of MDI containing Cold-Box P2 to be reduced in relation to the resin. The typical binder ratio for the Sipurid system is 60 % P1 and 40 % P2. Surprisingly, the viscosity of the base resin is lower, despite the resin’s higher molecular mass. This makes it possible to use significantly less solvent than with the previously generations of Cold-Box resins (Fig. 3).
Due to its high content of inorganic components, the Sipurid system represents the link between existing technologies and future inorganic core production. The carbon content is 20 - 25 % lower than aromatic Cold-Box systems and, thanks to the consistent incorporation of inorganic components, the Sipurid binder generation has already achieved an impressive inorganic content of 12.4 percent (Fig. 4). The primary objectives in the development of the Sipurid system were to further improve the Cold-Box process’s environmental compatibility and to minimise the emission of carbon and other pollutants. Due to its low organic load, very low levels of benzene, gas and condensates are emitted. Another major advantage is the significant reduction in smoke formation during and after casting.
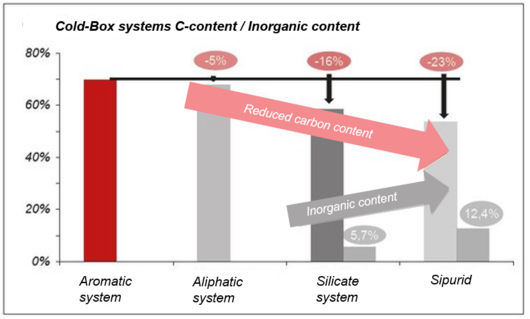
Housing for electric drive with integrated water and oil cooling circuits
The ready-to-install water-cooled electric motor housing (see lead picture) from DGH Sand Casting provides an excellent illustration for the challenges and potential solutions, as well as the opportunities to achieve significant synergy effects that result from a development partnership between foundries and a specialised foundry chemistry supplier. DGH Sand Casting, which is based in Friedrichshafen, Germany, has produced many millions of high-end castings for demanding customers since 1913. Over the years, the company has amassed comprehensive sand-casting expertise and offers a very broad range of cast products.
Background and requirements
Given intense cost pressure and a very tight schedule, the only process that ever really came into question was sand casting, which also happens to offer a high degree of design freedom with limited modification outlay in terms of time and cost. The customer was looking for a corrosion-resistant housing made from the alloy GAlSi7Mg0.3 AC 42100, the highest integration of functions through the use of cores, which allow almost infinite design possibilities and yet high-power density with the lowest installation space requirements (achieved through minimal wall thicknesses). Additional specifications included the best possible cooling through a “rough” water jacket surface, the best thermal stability in start-up operation and the integration of the gear oil balance with temperature control.
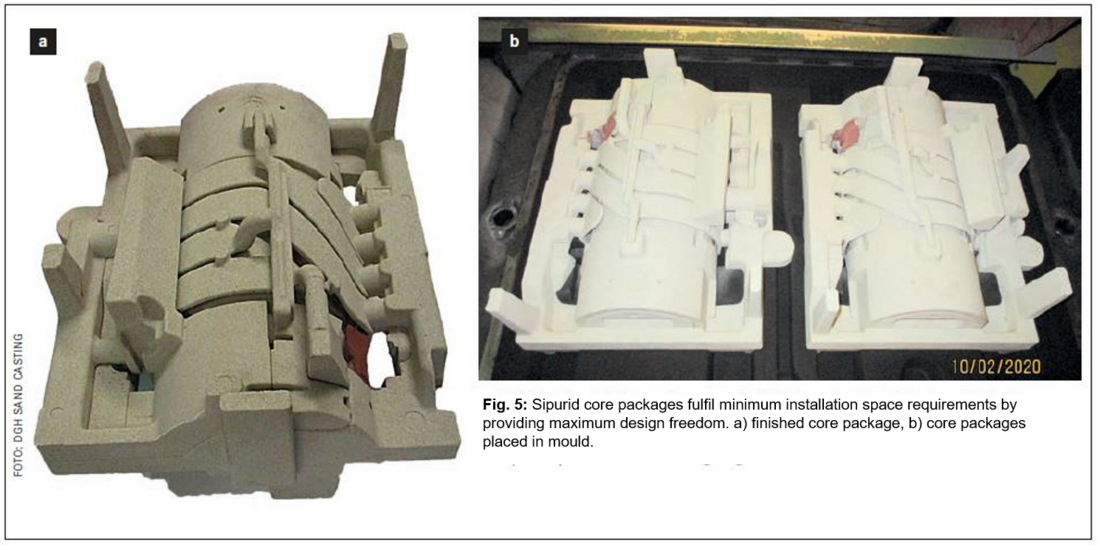
The solution
The DGH solution integrates the water and oil cooling circuits in a single housing. This fulfils the customer’s requirement for minimum space by exploiting the maximum design freedom offered by the sand-casting process (Fig. 5). Machining of the stator space is facilitated by cylindrical cores. Due to a reduction in tooling construction times, overall development times are shorter and tooling costs are lower than with permanent mould processes. Furthermore, the castings also achieve a high level of corrosion resistance and exhibit good mechanical properties.
Casting implementation
The electric drive housing won the 2019 Newcast Award for “Casting with the best functional integration”. The success of the casting is due to:
- reducing wall thicknesses to achieve the lowest possible weight
- positioning the sand cores to achieve optimal water jacket cooling
- casting simulations to achieve controlled solidification
- alloy selection to achieve corrosion resistance
- filling simulation for core boxes
Innovation of the Sipurid system
The previous binder system regularly “fogged” the production hall, especially in the shake out area. DGH Sand Casting was therefore looking to reduce smoke formation. After introducing the Sipurid system, the situation in the hall improved significantly. Compared to standard Cold-Box systems, Sipurid exhibits a higher thermal stability and a lower tendency to deformation (Fig. 6).
These desirable properties speak for themselves and also satisfied the foundry. By using the Sipurid system, tolerances in the deformation-critical water jacket areas were significantly better complied with (Fig. 7).
Summary and outlook
Thanks to the excellent technological work at DGH Sand Casting and the company’s development partnership with HA, complex components can now be manufactured more reliably and to higher quality standards than ever before. The example of the electric drive housing perfectly illustrates how the foundry industry can successfully satisfy new regulatory requirements. Since its introduction, the Sipurid system has undergone continuous development to ensure that it always more than meets the latest challenges. Our thanks go to DGH Sand Casting for their close collaboration, for providing the above data and for allowing us to publish this paper.
December 2020
Authors:
Peter-Michael Gröning, Regional Product Manager EMEA Cold-Box Systems, Hüttenes-Albertus Chemische Werke, Düsseldorf
Florian Piehler, Head of Technical Projects AV & Simulation, DGH Sand Casting Production GmbH & Co. KG, Friedrichshafen, www.dgh-sandcasting.de