One call to success: more efficient Cerabeads regeneration for 3D printing processes
The additive production of sand cores and sand moulds using the 3D printing process is becoming increasingly important in the foundry industry. In addition to the frequently used fine quartz sand with a furan resin binder, other moulding materials are also being used more and more. These include the synthetically produced speciality sand Cerabeads.
The advantages over quartz sand are the physical and chemical properties of the speciality sands:
- Suitable for all types of casting
- Suitable for the following processes: PUR-Cold-Box, SO2-Cold-Box, mask moulding material, cold resin, Resol-CO2 /MF, Resol/Ester
- Very low linear expansion coefficient
- Suitable for high thermal stress
- Selection of the optimum classification for the application possible
- Special types for sand pressure
Depending on the customer's requirements and the respective castings, the quality characteristics of the moulding material and therefore the quantity of activator used can vary - a decisive factor for successful regeneration.
In many cases, it is sufficient to sieve the removed moulding material after the printing process so that it can flow back into the job box for the next cores. Minimal residues of the activator can remain on the sand grain, which can be re-wetted in the next printing process. Depending on the casting, however, the use of previously used job box moulding material may not be suitable due to its low tolerance to gas defects.
3D printing and regeneration under one roof
The prototype and small series light metal foundry Becker CAD-CAM-CAST (Becker CCC) in Steffenberg-Quotshausen has been using large quantities of the synthetic moulding sand Cerabeads from Hüttenes-Albertus for years to produce complex 3D prototypes.
However, the regeneration process was previously carried out externally. The time-consuming transport of large quantities of special sand for a simple heating process seemed inefficient.
Guided by the vision of making the regeneration of Cerabeads significantly more efficient, energy-saving and therefore also much more environmentally friendly, the question quickly arose:
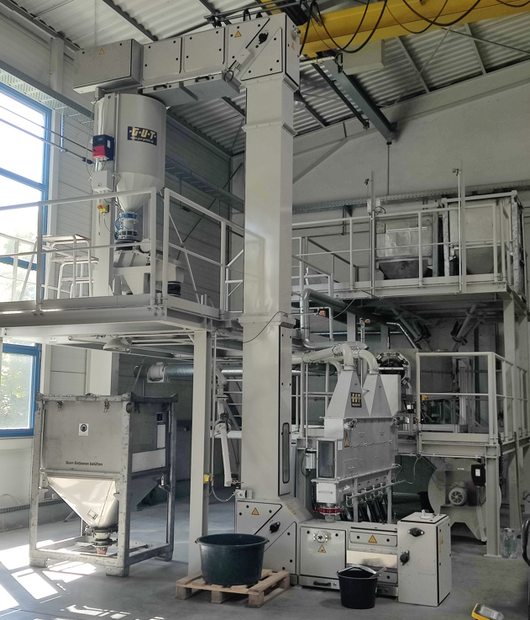
Why not regenerate ourselves?
The success story began in 2020 with a phone call between Ralf Dehnert, Head of Small Series Production at Becker CCC and specialist in automation and mechanical processing, and Martin Dahlmann, PM Hot Curing Systems & Special Sand and expert in regeneration.
With a small electric rotary kiln for calcining very small quantities in mind, the idea was born to install a similar kiln on site at Becker CCC. The planned regeneration plant would largely remove the activator from the Jobbox moulding materials already in use, making them usable again in almost the same quality as new moulding material.
It would also be possible to operate the plant with solar energy and thus save large amounts of CO2. The task to be accomplished in this joint project was to regenerate a maximum of 150 tonnes of Cerabeads per year at approx. 900°C.
After the idea had been allowed to develop for a few months, the concept was further developed in August 2021 by a team from Becker, G-U-T (foundry plant engineering) and HA. In collaboration with a furnace manufacturer, the first regeneration tests were successfully carried out shortly afterwards. The results were more than satisfactory and Becker CCC decided to install an electrically heated rotary kiln with a throughput of around 100 kg per hour, which means up to 2.4 tonnes of reclaim per day.
The system has now been running smoothly for over 18 months. The ExOne printer works perfectly and exclusively with this reclaim. From the initial idea to the installation of the system and the final Cerabeads regeneration, the joint project was a complete success for everyone involved.