Coatings for additively manufactured moulds and cores
3D printing gives designers unprecedented freedom in designing moulds and cores. Since printed cores differ significantly in some important properties from blown cores, there are specific requirements placed on the coatings. HA has developed a special series of Arkopal RP (Rapid Prototyping) coatings for the 3D printing process, which are already successfully being used for actual cast parts. They provide a smooth surface free of casting defects in aluminium, iron and steel castings.
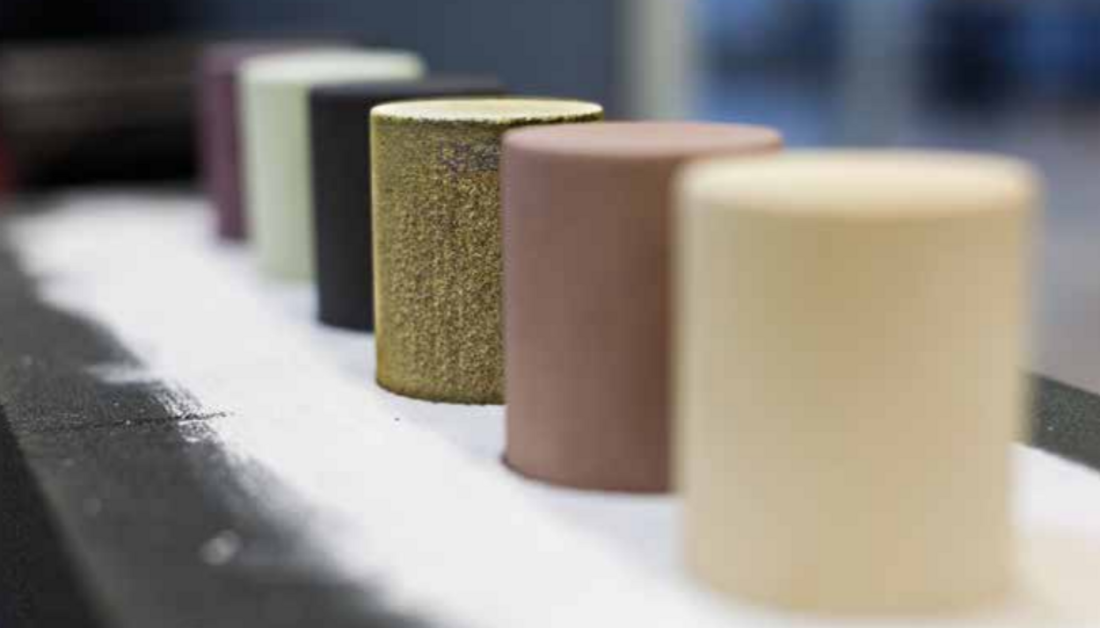
In the foundry industry, additive manufacturing makes it possible to produce prototypes and small batches without incurring high tooling and storage costs. Moulds and cores are preferably produced using the binder jetting process. Printed sand cores however, have particular process-induced prop-erties. This means that products specially adapted to the process are required. Printed cores and moulds are generally used in coated form not only in steel and grey cast iron casting, but also in aluminium casting.
Both the special surface structure and the complexity of printed cores require coatings with distinct application properties. At the same time, the coatings themselves must be highly effective against casting defects such as penetration or finning (veining).
The axis-dependent strength and compaction of the sand layers, as well as the surface structures of the poured and subsequently resin-bonded moulding materials also play an important role. The axis-dependent differences in strength lead, among other things, to an increased susceptibility to finning. Using commercially available coatings, finning can be reduced, but often not satisfactorily avoided. In order to find suitable solutions, the coating properties must be specifically adapted to the special properties of additive moulds and cores.
The following shows a variety of examples to demonstrate the effectiveness of the innovative Ar-kopal RP coatings developed by HA to avoiding casting defects such as finning, when casting addi-tively manufactured cores.
What is additive manufacturing or 3D printing?
Various processes are in use in the field of additive manufacturing. One of these methods is the binder jetting process. In this additive manufacturing process, cores or moulds are produced using a one-component or two-component binder system and a desired sand.
In the case of the two-component binder system, the sand is first coated with the activator in a mixer. The recoater then applies 4-8 layers of sand to the bottom of the moulding box.
When using a single-component system, unbound sand is used in this process step.
The print head then selectively prints a first layer of binder on the activated or unbound sand. In the single-component system, a heating lamp is additionally used on the recoater to accelerate the hardening process. The building platform in the job box is lowered by one layer and another layer is applied. After finishing a layer, the process starts again and is repeated until the core or mould is completely printed. Once the printing process is complete, the unbound sand is removed from the job box using an industrial vacuum cleaner, brushes and compressed air. The core or mould is then removed from the job box and, if necessary, post-hardened until the final strength is reached. Depending on the binder system used, the loose sand can be reused.
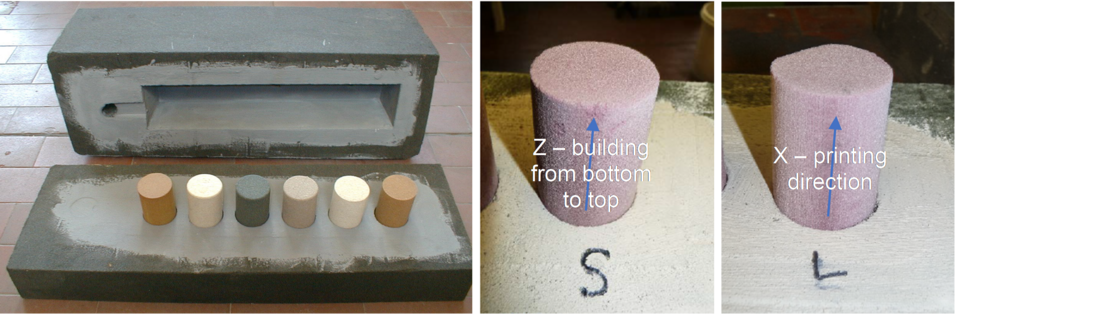
Arkopal RP (Rapid Prototyping): Product Development and Studies
HA’s Center of Competence, in the course of the development of special coatings for 3D printing, has thoroughly examined the role of coatings in printed cores and how to comply with the special requirements of the 3D printing process.
In the first step, the coatings for additively manufactured moulds and cores were characterised in benchmark tests for iron and steel casting. For this purpose, test moulds developed to demonstrate finning (see Figure 1) were used in order to be able to better compare the defect pattern on the cast parts after casting.
To additionally examine the impacts of the printing direction, the cores were each printed in two different directions: vertical and horizontal (see Figure 1).
The casting was produced in the first benchmark test with iron at a casting temperature of approximately 1430°C. The sample compression style cores were manufactured in accordance with HA specifications (diameter 50 mm). The average grain size of the sand used was 0.14 mm (sand GS 14) and the annealing loss was 1.43% – using a phenol-containing binder as a one-component system. The strength value achieved in the x-direction was 520 N/cm2, in the y-direction 430 N/cm2 and in the z-direction 190 N/cm2. After casting, the iron parts were sectioned in halves and cleaned of adhering sand residues with compressed air. The following pictures show one of the sectioned halves with the surfaces on the core side.
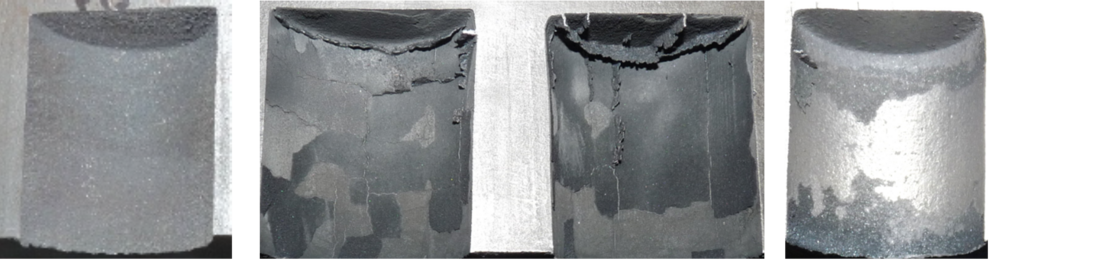
Influencing factors: packing density and printing direction
During the tests, it was found that the uncoated cores had no casting defects after casting, such as finning (see Figure 2, left). In the conventional core shooting process, the finning is caused by a high packing density of the sand grains, combined with other parameters. During the casting process, the phase transition from alpha- to beta-quartz takes place and the sand grains need space to expand [2].
With printed cores, on the other hand, the packing density is not as high as with shot cores as the sand is applied in layers. The packing density depends on the printing direction, and the resulting strengths after the binding process also depend on the printing direction. When uncoated cores are used, however, the cast surfaces are very rough due to the sand structure (see Figure 2, left).
The study showed that the formation of finning depends on the one hand on the core geometry and on the other hand on the printing direction (see Figure 2, middle).
In further experiments, it was found that several factors play a major role in suppressing the tendency of finning: the printing direction, the core geometry, the application method, but also the composition and the layer thickness of the coating.
The test results show that the casting defect is significantly less pronounced when brush applied compared to dipping (see Figure 3). One reason for this is suspected to be the penetration behaviour of the coating into the core. In general, it is proven that higher layer thicknesses provide a better casting surface with the same application characteristics.
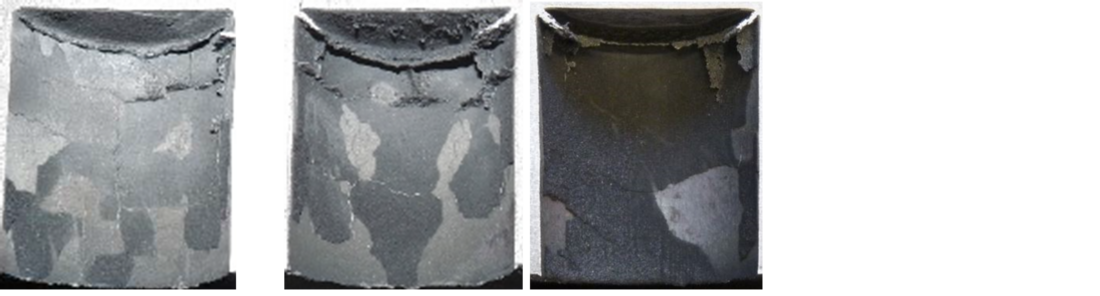
Other influencing factors: Application method and layer thickness
In further experiments, it was found that several factors play a major role in suppressing the tendency of finning: the printing direction, the core geometry, the application method, but also the composition and the layer thickness of the coating.
The test results show that the casting defect is significantly less pronounced when brush applied compared to dipping (see Figure 3). One reason for this is suspected to be the penetration behaviour of the coating into the core. In general, it is proven that higher layer thicknesses provide a better casting surface with the same application characteristics.
Figure 3 shows: Left: casting surface after coating by painting (layer thickness = 200 µm). Middle and Right: casting surface after coating by dipping (layer thickness middle = 200 µm, right = 300 µm); Conventional water-based zirconium coating:
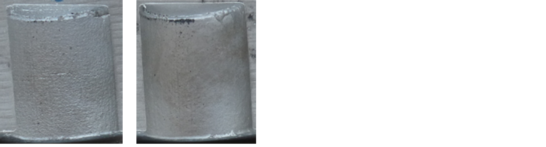
Right: casting surface (coated core, 800 µm)
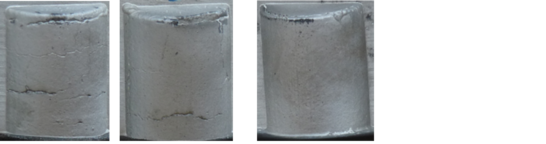
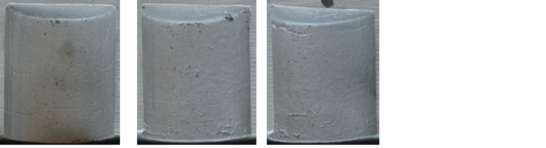
Application in steel casting
In steel casting, the requirements for the coatings are similar to those in iron casting, but an even higher temperature resistance is required. Steel is usually cast between 1480 and as high as 1750°C. The experiments once again used special test moulds developed to demonstrate finning (see Figure 1, left) and round compression cores. The sand mixture contained in this benchmark test was also GS 14, but a two-component furan binder system was used.
The test mould was cast at approximately 1480°C. The results show that in the case of uncoated cores, there is only a small finning tendency combined with sand adhesion (see Figure 4). The surface roughness of the uncoated cores was at an Ra value of approximately 10 µm. In the case of coated cores, the surface roughness was between 3-5 µm – depending on the respective coating composition and the layer thickness achieved during application.
In view of the test results, it could also be seen that in steel casting, in parallel with iron casting, both the direction of pressure and the layer thickness play a major role in the occurrence of casting defects. In tests also carried out at the HA Center of Competence, more finning was detected in the vertical printed cores (S cores) than in the horizontal printed cores (L cores).
Additionally, the higher layer thicknesses produced significantly smoother (Ra value of 3-4 µm) and defect free surfaces could be achieved with regard to finning. In principle, the use of a perfectly matched coating greatly minimises both finning and sand adhesions.
Application in aluminium casting
The study included only a small number of tests with printed cores in aluminium casting. It was observed that the situation for the casting of aluminium is significantly different because of the lower casting temperatures of 660-750 °C no finning (veining) occurs. Generally, conventionally manufactured cores for aluminium parts are often not coated at all. Due to the smooth core surface, acceptable casting surfaces are achieved here even without a smooth protective coating layer.
However, cores produced using the 3D printing process have significantly rougher surfaces and layer grooves from the printing process. After casting, the casting surface is also correspondingly rough. In order to achieve a smooth casting surface, it is therefore advisable to coat the cores or moulds before casting. Sand adhesion can also be avoided by applying a coating.
Summary
The use of different coatings for additively manufactured cores and moulds revealed significant variations in the casting results. Due to the axis-dependent strengths, the uncoated cores achieve positive results with regard to casting defects such as finning. However, the use of coatings specially developed for 3D printing can prevent the formation of rough casting surfaces and sand adhesion.
The study carried out at HA has shown that several factors in the 3D printing process have an influence on the casting defect characteristics. The core geometry and the printing direction play an important role in iron and steel casting. According to our findings, the finning is more pronounced in a vertically printed core compared to a horizontally printed core. The chemical composition and processing properties are important criteria for coating selection with regard to avoiding casting defects. The application process and the resulting layer thickness also play a role. With the aid of the optimum coating, casting defects such as finning (veining) can be avoided and smooth casting surfaces can be produced.
Due to the lower casting temperatures, other requirements for the coatings are important in aluminium casting. The focus here is on surface quality and the avoidance of sand adhesion. The surface quality is strongly influenced by the printed core. By using special coatings, sand adhesion can be minimized and smooth surfaces achieved.
The findings described above have been incorporated into the development of Arkopal RP (Rapid Prototyping) series coatings. Foundries that use 3D printing for their moulds and cores can rely on products specifically developed for the process. The coating experts at HA will be happy to advise you.
Published: Okober 2019
Author: Dr.-Ing. Ekaterina Potaturina, Produkt Manager Coatings, Hüttenes-Albertus Chemische Werke GmbH, Düsseldorf und Dr. Klaus Seeger, Chemiker, Hüttenes-Albertus Chemische Werke GmbH, Hannover.