Filtration
Filtration of molten metals in foundry processes is a widespread and mandatory practice to produce inclusion-free castings. The presence of any inclusions (exogenous and/or endogenous) compromises the mechanical properties of the castings and often causes scrap.
Exogenous inclusions: residual reaction products arising from the treatment of the liquid metal; metal / refractory reaction products.
Endogenous inclusions: green sand inclusions due to entrapment and/or erosion of moulds or cores; filter particles; oxidation of the metal due to turbulence during the filling; ferroalloy residues from In-Mould treatment and/or inoculation; incompletely melted inoculants or ferroalloys; residues of additives.
HA Italia has developed a complete range of extruded and foam filters for every type of application: ferrous and non-ferrous, automatic and manual moulding, horizontal and vertical parting line, green sand, chemically bonded sand and metal moulding.
HA Italia filter systems are now applied in the best foundries in the most varied sectors, such as automotive, hydraulics, industrial vehicles, agricultural and construction machinery, wind power/energy, various mechanics and many others.
Celtef extruded ceramic filters
Celtef Extruded Ceramic Filters, thanks to the technical ceramics with high chemical-physical characteristics developed in HA Italy, combined with the special filter production system, guarantee the best ratio between filtering efficiency and low pressure drop of the metal flow. HA Italia Extruded Filters can be used in any application and with any moulding plant: automatic or manual, with horizontal or vertical parting line, with green sand or chemically bonded sand.
Celtef filter technology responds optimally to customer requests, offering:
High filtering efficiency in applications for ductile, gray, malleable cast iron and high or low alloyed cast iron
Maximum filtration of the slag present in the molten iron as well as the sand particles and all the non-metallic inclusions carried by the flow and of the only partially melted inoculants
Extreme precision and dimensional constancy of the filter cells, which guarantee the stability of the flow and transform its motion from turbulent to laminar, thus preventing the formation of metal oxides and erosion of the mould
High mechanical strenghts
Easy to use and to apply
CELTEF Technology, due to its special physical-chemical filtration mechanism, meets the high quality standards required by the foundries in several sectors and applications. For this reason, CELTEF Technology represents a safe and economical solution for achieving an optimal level of casting quality.
Foam ceramic filters
Available in different ceramics based on silicon carbide (SiC), zirconia (ZrO2), alumina (Al2O3) and graphite and with different levels of porosity, the foam filters are suitable for the filtration of ferrous and non-ferrous metals in all moulding systems.
The particular conformation of the foam structure of the filter, made up of interconnected and dodecahedral shaped pores, gives the metal flow continuous fluctuations in direction and speed. This behavior of the liquid metal inside the pores favors the deposition of inclusions in the various interstices inside the filter.
Foam filters are available with a different degree of pore distribution (filter porosity): 10, 20, 30 ppi (pores per linear inch). The choice of the filter and the correct filter porosity is fundamental for the filtration of the different metals at the different operating conditions and for obtaining castings without inclusions.
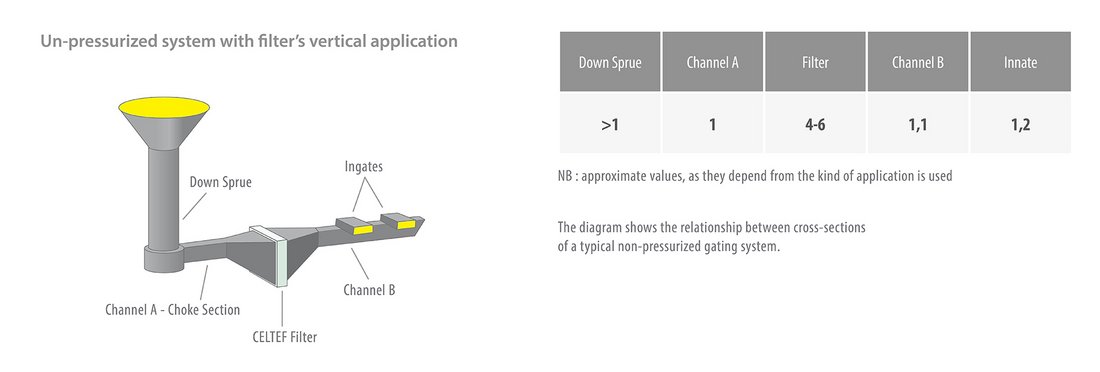
The ceramic filters can reach the highest levels of technical and economical performance if applied with a correct gating system and with a correct filter print design.
It is strongly recommended to apply the ceramic filters to a non-pressurized gating system, where choke section is located after the downsprue and just before the filter housing and the position of the other components is the following:
- runners positioned fully in the drug
- gates positioned fully in the cope