Proven future technology
This is not a contradiction: The Cold-Box process has been the leading core production process for series casting for 50 years. In sync with the further advances in castings for highly developed consumer markets, HA, as one of the leading foundry chemical suppliers, has continuously optimised its binder systems ever since. A comprehensive product range is now available especially for the Cold-Box process, so that foundries can always find the optimum binder solution depending on the area of application and their individual requirements.
HA's Cold-Box binder systems strike the perfect balance: lower emissions and uncompromising performance.
The Strengths of Cold-Box Technology
The Cold-Box system owes it position as the leading core production process to its wide range of applications, efficiency and cost-effectiveness. Excellent strength properties and very good dimensional accuracy mean that Cold-Box cores meet the growing demands placed on modern castings. Special technical criteria, such as elasticity, thermal stability and low gas generation, have also been continuously optimised.
Production-related advantages from the foundries point of view:
- No heated core box required
- Flexibility when selecting the tooling material (plastic, wood, metal)
- Proven, robust process
- Fastest possible cycle times
- Optimal decomposition properties
- Good reclaimability of core sand
- Excellent shelf life of cores
- Lowest binder addition
Focus of Development: Improved Environmental Properties
An increasing challenge for foundries, however, is meeting ever stricter environmental requirements. Since emissions in the Cold-Box process are inherent to the system, efforts to further develop Cold-Box binders have focused not only on technological optimisation but also on improving environmental properties. For more than three decades, the research department of Hüttenes-Albertus has been dedicated to reducing the environmental impact and emissions from its products. Our research and development aim to reduce emissions step by step through the reduction of organic components.
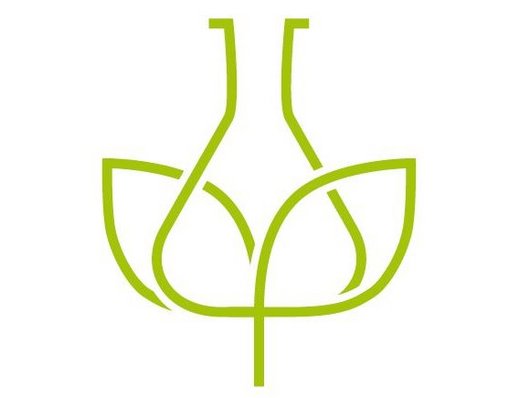
Solution Approaches
- Performance improvement to allow for reduced quantities of additives
- Replacing aromatic solvents
- Substitution of aromatic solvents and other harmful ingredients
- Use of inorganic elements in organic binders
- Use of additives that „capture and neutralise“ contaminants
HA has successfully pursued all these paths in product development over recent years and decades, resulting in our four product types: Sigmacure, Biocure, Silcure and Sipurid.
Biocure: Over 20 Years of Experience with Plant-Based Solvents
In 1996, HA was the first supplier in the world to launch a patented, more evironmentally friendly Cold-Box alternative, which enabled both a reduction in odour emissions during core production and a significant reduction in BTX values (benzene, toluene, xylene) after casting. HA has replaced the aromatic solvents in Biocure products, for example, by using methyl esters that are obtained from plant-based, renewable raw materials such as rapeseed. Since the chained (aliphatic) molecules contain more hydrogen and less carbon, CO2 emissions are also reduced.
- HA is the only manufacturer with more than 20 years of experience with plant-based CB
- Use of renewable raw materials
- Reduced BTX, BTEX und CO2 emissions
- Reduced odour during core production
- Reduced catalyst consumption
- Superior seperation of core and tool
- Elemination of casting defects such as erosion and scabbing due to high heat resistance
- Excellent dimensional accuracy
- Particulary suitable for casting in bentonite-bonded moulding material.
Sigmacure: A Robust Classic
Sigmacure is the universal classic product: a Cold-Box binder system in which the two components, phenolic resin and polyisocyanate, come dissolved in aromatic solvents. This system provides foundries with a product line whose efficiency is based on decades of experience.
- High productivity, fast cycle times
- Good processability, good sand durability even with moderate sand quality
- Moisture resistand, even under difficult climatic conditions
- Many customised variants for special requirements
- Suitable for any existing equipment
- High process safety
Silcure: Inorganic Elements in Solvent
In 1999, HA introduced Cold-Box systems with shares of silicate-containing solvents to the foundry industry. These solvents contain Si compounds in the molecule instead of hydrocarbons. A lower carbon content results in reduced BTX, BTEX and CO2 emissions.
- High thermal stability
- Very low condensate formation, thus less cleaning effort
- Low gas formation, thus fewer casting defects (scabbing, gas defects, pinholes)
- Very suitable for die casting
Sipurid: Inorganic Elements in Solvent and Resin Body
HA has consistently pursued the path of organic reduction with the latest Cold-Box generation Sipurid. In addition to the silicate component in the solvent, the resin molecule was also modified: the conventional OH-groups in the resin were partially replaced by silicate elements.
- Cold-Box binder with the lowest BTX and BTEX emissions available on the market
- Lowest fume formation
- Minimum condensate formation
- Lowest gas evolution
- Excellent suitability for die casting
Theory and Practice
As demand for highly complex castings with ever more stringent quality requirements increases, it has become ever more urgent to solve the pressing issues of resource conservation and sustainability. But achieving the highest levels of quality and environmental compatibility do not have to be mutually exclusive. Hüttenes-Albertus supplies proven and continuously refined Cold-Box quality. Read more about how our products help foundries save resources and the success of our tailor-made solutions.