RESISTENCIA A FLEXIÓN, TRACCIÓN Y DUREZAS, ¿QUÉ MÉTODO USAR?
Una importante labor del fundidor es asegurar unas propiedades adecuadas en sus moldes de arena. Este artículo tiene por objeto analizar los tres métodos más utilizados para el control de calidad de los moldes aglomerados químicamente, así como mostrar un estudio de laboratorio que intenta relacionar estos valores.
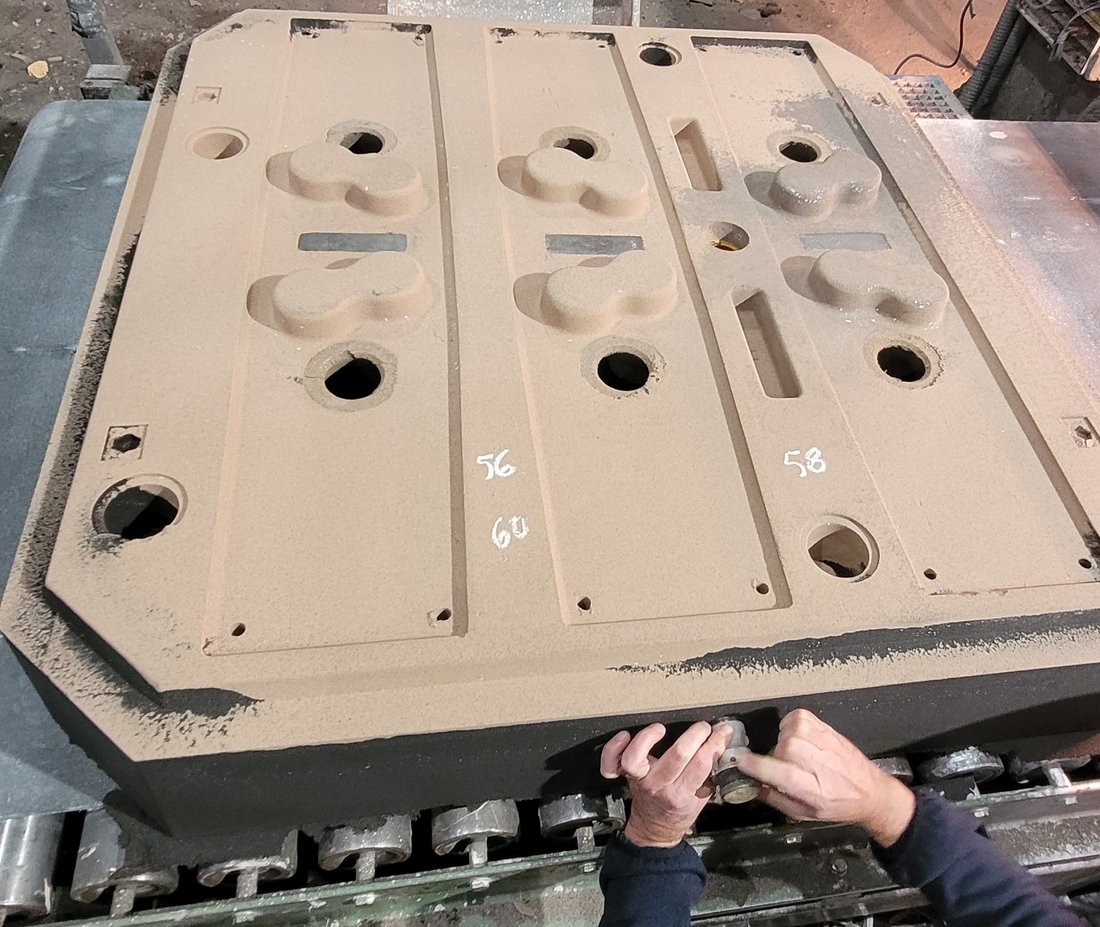
Por: Alex Zalloetxebarria Esnal
Situación del moldeo con arena en la península ibérica
Actualmente el 75% de las piezas fundidas en la península se fabrican utilizando moldes y machos de arena. Para ello, en las fundiciones de España y Portugal se aglomeraron, durante el 2024, aproximadamente 2.600.000 toneladas de arena.
Con relación a la tipología de estas arenas, el mayor volumen se corresponde con arenas recuperadas; arenas previamente usadas y reacondicionadas en las propias plantas. La arena nueva de sílice (cuarzo) supone el 15% del total de la arena aglomerada y se emplea fundamentalmente para refrescar los circuitos y para la fabricación de machos disparados. El origen de esta arena nueva de sílice es casi siempre peninsular, por suerte contamos con muy buenos yacimientos. Las arenas especiales (aquellas que no son de sílice) representan alrededor del 0,6% del volumen total. Estas arenas, debido a su carestía, se destinan solamente a moldes donde se requieren características térmicas y/o mecánicas diferentes. Existen varios tipos, siendo la arena de cromita sudafricana la que más se utiliza.
Aproximadamente, la mitad de todo este volumen de arena se conforma mediante de la técnica fisicoquímica de moldeo en verde y la otra mitad a través de procesos químicos de aglomeración. En este artículo se tratarán aspectos relacionados con las técnicas puramente químicas.
La complejidad de controlar un molde aglomerado químicamente
Como es sabido, la calidad del molde de arena es clave para la obtención de piezas sanas y una de las labores del fundidor es asegurar unas propiedades adecuadas. A veces, al técnico le pueden surgir dudas de cómo hacerlo, de hecho, suelen llegar consultas en este sentido. El objetivo de este escrito es intentar arrojar cierta luz acerca de este tema y comparar los tres métodos más utilizados actualmente; la dureza “scratch”, la resistencia a flexión y la resistencia a tracción. Los comentarios y análisis se refieren a procesos químicos autofraguantes como el furánico, el fenólico-uretano, el alcalino “alphaset” y el de silicato-éster, si bien, hay muchos conceptos que son perfectamente extrapolables a los procesos de caja fría y a los de caja caliente.
La primera recomendación, y probablemente la más importante, es que tenemos que estar abiertos a posibles dispersiones y/o resultados inesperados debido a los siguientes factores:
- La arena es un material heterogéneo. Un kilogramo de arena de sílice, de finura AFS 50 por ejemplo, contiene aproximadamente 30 millones de granos, todos ellos distintos.
- En la conformación de un molde por vía química, estamos creando un composite de un material inorgánico (> 97% de arena de sílice) y otro orgánico (aglomerante químico). Los procesos de mezclado y compactado influyen muchísimo en la homogeneidad del molde.
- La temperatura de la arena es una variable importantísima y no siempre es la misma en todas las partes del molde (núcleo, superficie, contacto con la caja…). A esto hay que añadir que también afectan otros parámetros externos como la temperatura y la humedad ambientales.
- Las propiedades del molde no son constantes en el tiempo, sino que evolucionan conforme avanza la polimerización de la resina. La resistencia y la dureza consecuentemente siguen curvas, ascendentes al principio y más planas después. No suele ser habitual que las curvas sigan tendencia ascendente transcurridas 15 horas.
- Si se estufa el macho o molde, se cambia radicalmente la curva de resistencia. El proceso de polimerización se acelera y se alcanza el máximo de resistencia mucho antes. Generalmente tras salir de la estufa y enfriarse, el molde ya ha alcanzado su resistencia máxima.
Por consiguiente, el control de la calidad de los moldes es más complejo de lo que parece. Censores como la incertidumbre y la dispersión entre los resultados estarán siempre intentando desanimar al técnico. No obstante, si se realiza con la debida cautela y atención, la información que se consigue es muy valiosa y provechosa.
Tres métodos muy utilizados
Con relación a los métodos utilizados en la actualidad para el control de la calidad de los moldes de arena, los más empleados son la dureza “scratch”, la resistencia a flexión y la dureza a tracción. Cada cual con sus ventajas e inconvenientes.
La dureza “scratch” mide la resistencia que presenta la superficie del molde a ser penetrado por una fresa de 9 mm de diámetro. Sus ventajas más notables son:
- El durómetro se maneja manualmente y es de pequeñas dimensiones, se puede llevar incluso en el bolsillo de la chaqueta.
- Permite tomar durezas en cualquier zona del molde sin apenas dejar marca. Generalmente, los técnicos prefieren tomar las mediciones en zonas que no se corresponden con pieza.
- El equipo necesario, el durómetro o rascador “scratch”, es muy asequible económicamente, su coste ronda los 1.200 €.
En cuanto a sus inconvenientes, se podrían destacar los siguientes:
- La medición refleja la dureza de un área relativamente pequeña (0,63 cm2), prácticamente un punto, por ello, los resultados obtenidos con esta herramienta suelen presentar dispersión. Se recomienda tomar durezas en varios puntos y trabajar con valores medios.
- Con este ensayo se mide solamente el estado superficial, no la del núcleo. Hay que indicar que en el proceso furánico, por ejemplo, las partes expuestas al aire endurecen más rápidamente que las del interior.
Por otro lado, las resistencias mecánicas a tracción y a flexión también nos sirven como indicadores de la calidad de un molde aglomerado químicamente. En Europa se emplea sobre todo la resistencia a flexión, aunque hay también fundiciones que utilizan las probetas a tracción. El segundo método está más extendido en el continente americano.
Las principales ventajas de ambos métodos son:
- Recogen información de una zona bastante amplia (5 cm2) y los resultados suelen ser menos dispersos.
- Existen resistómetros automáticos que eliminan el factor humano a la hora de romper las probetas.
También hay inconvenientes:
- El resistómetro de arenas es un equipo sensible y pesado que debe alojarse en un lugar adecuado; en un laboratorio o por lo menos en un habitáculo libre de polvo. Se trata de un equipo caro, se podría decir que quién tiene uno de ellos, aunque sea manual, tiene una joya.
- Las probetas y el molde son cuerpos separados y si no se toman las medidas oportunas estas pueden no reflejar la realidad del molde. Probetas y molde pueden compactarse con distinto grado de intensidad e incluso en momentos diferentes. Las probetas, por su tamaño, tenderán a adquirir la temperatura ambiental o la del probetero, mientras que la temperatura del molde rondará la del silo de donde procede la arena.
Rotura a tracción
Existe también una tercera variante de resistencia, la de la rotura a compresión, muy habitual en moldeo en verde, pero poco o nada usada en moldeo químico. Esta variante solamente se usa en algunos países asiáticos y requiere de un equipo de rotura de probetas muy potente. En HA Ilarduya se utiliza la versión a flexión dado que es la que menor dispersión presenta entre resultados.
Relacionando resistencia a flexión, a tracción y durezas:
Recientemente se ha realizado un estudio en el laboratorio en HA Ilarduya con objeto de averiguar si existe relación entre los valores de dureza y resistencia en los moldes de arena aglomerados químicamente. La tarea ha consistido en confeccionar en paralelo probetas a flexión y a tracción. En este caso, se han realizado mezclas con arena nueva de sílice y diferentes cantidades, desde el 0,60 al 1,20%, de resina furánica. Tras una espera de 24 horas en el laboratorio, se mide en el mismo momento la dureza scratch, la resistencia a flexión y a tracción de las probetas. En total se obtienen 192 valores, los cuales han permitido dibujar las curvas que relacionan los tres parámetros. En la gráfica se ha preferido dejar la resistencia a flexión en abscisas.
Comentarios y recomendaciones:
1. Cualquiera de los tres métodos es perfectamente válido para ayudarnos a conocer la realidad del molde. No obstante, por todo lo explicado anteriormente, el fundidor, de acuerdo con las características de su planta, deberá definir dónde, cuándo y cómo realizar las mediciones. Sin duda, será la liturgia la que nos permitirá recibir el mensaje verdadero.
2. En cuanto a los valores recomendados en el momento del vertido metal, no hay una guía al respecto. Según nuestra experiencia, la resistencia a flexión debería superar los 200 Nw/cm2 (20 Kg/cm2).
3. Interesa también evitar resistencias excesivamente altas. Valores elevados son indicativos de un gasto innecesario de aglomerante, una mayor evolución gaseosa y en el caso del proceso fenólico uretano, un mayor riesgo de veining (cola de rata). Por ello, recomendamos marcar un límite superior en la resistencia a flexión, creando una horquilla de trabajo de 200 - 320 Nw/cm2 (20 - 32 Kg/cm2). Las correspondencias aparecen en la gráfica.
Estas horquillas deben tomarse como una sugerencia general, habrá también seguro situaciones particulares. Por ejemplo, si se quiere mejorar el desarenado, es preferible trabajar con resistencias bajas y si el molde está expuesto a altas solicitaciones mecánica y/o térmicas, mejor apuntar hacia resistencias elevadas.
4. Recomendamos acompañar el dato de la dureza (o resistencia) con el del AFA, el LOI (pérdidas por calcinación) y con alguna información sobre la velocidad de fraguado del molde; por ejemplo, el de la vida de banco. Así tendremos un conocimiento ya más que importante sobre el ADN del molde.
Mención a:
-El personal de laboratorio de HA Ilarduya por su labor. (Raquel Quintana, Leire Abaitua, Lisa Aibar )
- Mikel Segundo Buezo , Arturo Galarza e Ignacio Martinez del Agua de SAKANA S. COOP. por sus iniciativas creativas entorno a las arenas.
- Santiago Martinez Masip MTG y Eugenio Sorazu HAIZEA Grupo WEC por cuidar tan bien sus circuitos de arena.
- Erika Garitaonandia AZTERLAN Metallurgy Research Centre por su predisposición.
- Italtractor ITM SpA (Pyrsa) por cesión de fotografías.